Engine piston blank and machining method thereof
An engine and piston technology, used in engine components, machines/engines, pistons, etc., can solve problems such as higher requirements for high-temperature fatigue performance, high risk of cracking failure, and throat fatigue cracks, so as to improve fatigue strength and reduce throat. The risk of cracking failure, the effect of refining the metallographic structure
- Summary
- Abstract
- Description
- Claims
- Application Information
AI Technical Summary
Problems solved by technology
Method used
Image
Examples
Embodiment Construction
[0024] The core of the present invention is to provide an engine piston blank. By setting the annular groove, failures such as throat fatigue cracks and head cracks can be effectively avoided, materials can be saved, and the quality of the finished piston product can be improved. Another core of the present invention is to provide a processing method for the above-mentioned engine piston blank.
[0025] In order to enable those skilled in the art to better understand the solution of the present invention, the present invention will be further described in detail below in conjunction with the accompanying drawings and specific embodiments.
[0026] Please refer to figure 1 and figure 2 , figure 1 It is a structural schematic diagram of a specific embodiment of the engine piston blank provided by the present invention; figure 2 It is a schematic cross-sectional view of a specific embodiment of the engine piston blank provided by the present invention.
[0027] The specific...
PUM
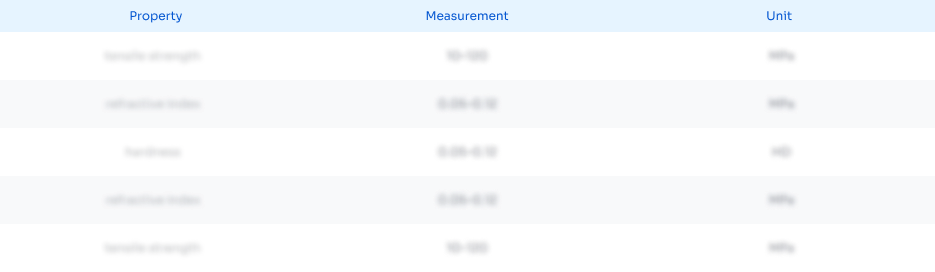
Abstract
Description
Claims
Application Information

- R&D Engineer
- R&D Manager
- IP Professional
- Industry Leading Data Capabilities
- Powerful AI technology
- Patent DNA Extraction
Browse by: Latest US Patents, China's latest patents, Technical Efficacy Thesaurus, Application Domain, Technology Topic, Popular Technical Reports.
© 2024 PatSnap. All rights reserved.Legal|Privacy policy|Modern Slavery Act Transparency Statement|Sitemap|About US| Contact US: help@patsnap.com