A self-locking folding unmanned aerial vehicle with stably rotating wings
A folding and unmanned aerial vehicle technology, applied in the field of unmanned aerial vehicles, can solve the problems of automatic locking, unreliable wing rotation, low stability and safety, etc., to reduce tilt or shake, reduce friction, The effect of improving stability
- Summary
- Abstract
- Description
- Claims
- Application Information
AI Technical Summary
Problems solved by technology
Method used
Image
Examples
Embodiment 1
[0037]A foldable unmanned aerial vehicle with stable rotation and self-locking wings, including a bulkhead 1, a plurality of mounting seats 2 are arranged on the bulkhead 1, a mounting hole 21 is provided in the middle of the mounting seat 2, and a machine tool is sleeved in the mounting hole 21. Wing rotating shaft 3, one end of wing rotating shaft 3 is connected with wing 4; Mounting seat 2 is also provided with bulkhead annular groove 22, and bulkhead annular groove 22 is concentric with mounting hole 21, and wing 4 is provided with wing annular groove 41, A torsion spring 5 is sleeved in the bulkhead annular groove 22, and the other end of the torsion spring 5 is sleeved in the wing annular groove 41. One end of the torsion spring 5 is engaged with the bulkhead 1, and the other end of the torsion spring 5 is engaged with the wing. 4 snapping; the mounting seat 2 is provided with a positioning installation hole 23, and a locking mechanism 6 is installed in the positioning in...
Embodiment 2
[0042] On the basis of Embodiment 1, L-shaped grooves 7 are arranged on the bulkhead 1 and the wing 4, and the L-shaped groove 7 on the bulkhead 1 communicates with the annular groove 22 of the bulkhead, and the L-shaped groove 7 on the wing 4 The groove 7 communicates with the annular groove 41 of the wing; both ends of the torsion spring 5 are bent into a hook 51, and the hook 51 near the end of the bulkhead 1 snaps into the L-shaped groove 7 on the bulkhead 1, close to the wing The hook 51 at one end of the 4 is snapped into the L-shaped groove 7 on the wing 4.
[0043] The hooks 51 at both ends of the torsion spring 5 are snapped into the L-shaped groove 7, so that one end of the torsion spring 5 is fixed relative to the bulkhead 1, and the other end of the torsion spring 5 is fixed relative to the wing 4, and the torsion spring 5 is in the process of torsion. The wing 4 can rotate relative to the bulkhead 1, so that the wing 4 is unfolded or retracted. The hook 51 is lim...
Embodiment 3
[0045] On the basis of Embodiment 1 or Embodiment 2, two bearings 24 are installed between the wing shaft 3 and the mounting hole 21, and a spacer 25 is set on the wing shaft 3, and the spacer 25 is located between the two bearings. Between 24.
[0046] The bearing 24 can effectively reduce the friction force when the wing 4 rotates, further improves the stability of the wing 4 during rotation, and reduces the situation that the wing 4 is tilted or shaken. The spacer 25 can separate the two bearings 24 to prevent the rollers of the two bearings 24 from rubbing against each other.
PUM
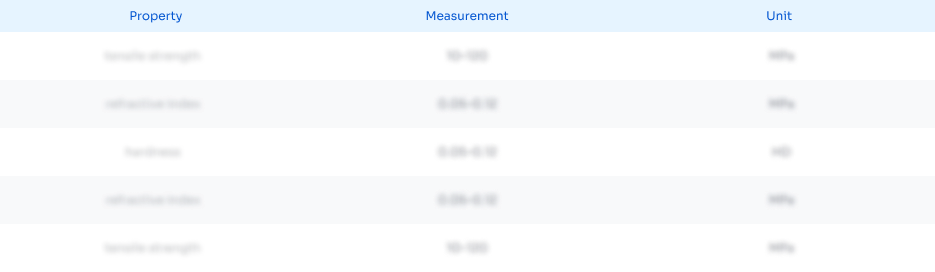
Abstract
Description
Claims
Application Information

- R&D
- Intellectual Property
- Life Sciences
- Materials
- Tech Scout
- Unparalleled Data Quality
- Higher Quality Content
- 60% Fewer Hallucinations
Browse by: Latest US Patents, China's latest patents, Technical Efficacy Thesaurus, Application Domain, Technology Topic, Popular Technical Reports.
© 2025 PatSnap. All rights reserved.Legal|Privacy policy|Modern Slavery Act Transparency Statement|Sitemap|About US| Contact US: help@patsnap.com