Multi-stage sleeve type lifting mechanism for robot
A lifting mechanism and sleeve-type technology, which is applied in the field of robots, can solve problems such as uneven lifting speed, large gaps and easy deformation, and mechanism loads that are easy to swing, so as to achieve simple and reliable transmission structure, neat winding arrangement, and ensure stability. Effect
- Summary
- Abstract
- Description
- Claims
- Application Information
AI Technical Summary
Problems solved by technology
Method used
Image
Examples
Embodiment 1
[0051] A preferred embodiment of the present invention provides a multi-stage sleeve-type lifting mechanism for a robot. The drive assembly includes a drive motor 1 with an adjustable drive speed, a reducer 2, and a synchronous pulley 15. The drive motor 1 is connected to the The speed reducer 2 is connected in transmission, and the speed reducer 2 is connected in transmission with the synchronous pulley 15, and the synchronous pulley 15 is connected with the reel 3 through the synchronous belt 16.
[0052] The working principle of this embodiment: the mechanism is driven by a motor, the reducer 2 decelerates, and then the rotational motion and torque are transmitted to the reel 3 through the transmission of the synchronous pulley 15, and the reel 3 winds or releases the flat belt 4 to The moving end of the mechanism (ie base plate 9) is lifted and released.
Embodiment 2
[0054] The present invention provides a multi-stage telescopic lifting mechanism for a robot on the basis of Embodiment 1. The drive motor 1 is equipped with an encoder and a brake capable of power-off braking.
[0055] The working principle of this embodiment: the drive motor 1 has its own encoder and brake, and the encoder is used to control the position of the moving end of the mechanism, to locate and repeat the positioning of the moving end; the brake is a power-off brake, which is used for sudden power failure and shutdown Always protect the moving end of the lifting mechanism from falling down due to gravity.
Embodiment 3
[0057] A preferred embodiment of the present invention provides a multi-stage sleeve type lifting mechanism for robots, one end of the flat belt 4 is connected to the bottom plate 9, and the other end passes through the innermost sleeve 8 and bypasses the flat belt bogie 5 After being wound on the reel 3, the length of the flat belt 4 can be cut according to actual needs. The material of the flat belt 4 is a stretch-resistant material, and the flat belt 4 is a polyester belt.
[0058] The working principle of this embodiment: the flat belt bogie 5 can prevent the flat belt 4 from rubbing against the sleeve, protect the flat belt 4 and reduce the winding resistance of the flat belt 4 . The winding length of the flat belt 4 is cut according to the actual required length, and the flat belt 4 can be cut according to the distance from the moving end of the mechanism to the ground. Because the length of the flat belt 4 has been adjusted, when the reel 3 has released all the flat bel...
PUM
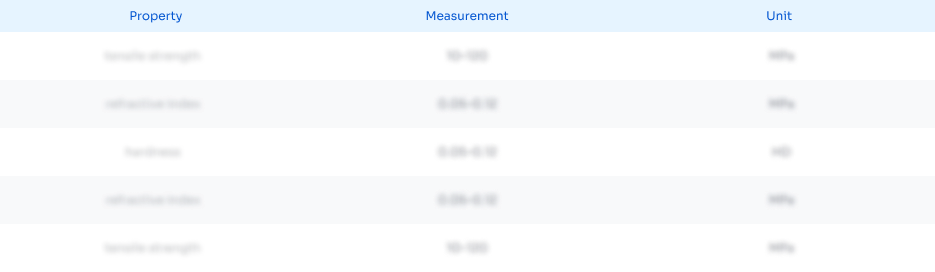
Abstract
Description
Claims
Application Information

- R&D
- Intellectual Property
- Life Sciences
- Materials
- Tech Scout
- Unparalleled Data Quality
- Higher Quality Content
- 60% Fewer Hallucinations
Browse by: Latest US Patents, China's latest patents, Technical Efficacy Thesaurus, Application Domain, Technology Topic, Popular Technical Reports.
© 2025 PatSnap. All rights reserved.Legal|Privacy policy|Modern Slavery Act Transparency Statement|Sitemap|About US| Contact US: help@patsnap.com