Distillation system and technology of ethylene glycol and diethylene glycol in polyol waste liquid
A diethylene glycol and distillation system technology, which is applied in the field of distillation system and distillation process, can solve the problems of high recycling cost, large interference, and low content, and achieve the effects of reducing environmental protection expenses, reducing load, and reducing content
- Summary
- Abstract
- Description
- Claims
- Application Information
AI Technical Summary
Problems solved by technology
Method used
Image
Examples
Embodiment 1
[0029] see figure 1, is a specific example of a distillation system for ethylene glycol and diethylene glycol in polyol waste liquid. The distillation system of ethylene glycol and diethylene glycol in polyol waste liquid includes a first rectification tower 1, a second rectification tower 2, and a vacuum device 3, and the first rectification tower 1 includes a first tower body 1a , the first reboiler 1b, the first condenser 1c, the first separator 1d, the first pump 1e, the second rectification column 2 includes a second column body 2a, a second reboiler 2b, a second condenser 2c, the second separator 2d, the second pump 2e, the first tower body and the second tower body adopt conventional packed towers, and the reboiler, condenser, separator and pump are all conventional chemical equipment on the market, wherein The separator adopts cyclone separator. The upper part of the first tower body 1a is connected with a feed pipe 4. In this embodiment, the feed pipe extends horizo...
Embodiment 2
[0031] Get 500ML waste liquid, detect by infrared analysis, diethylene glycol content is 21.87% in waste liquid, and ethylene glycol content is 49.62%, and 1.4BG (1.4 dibutanol) content is 27.49%, and surplus is a small amount of water and Polyester polyol.
[0032] Adopt embodiment one distillation system to separate the method for ethylene glycol, diethylene glycol in polyol waste liquid, have the following steps:
[0033] 1) Distill the waste liquid at 100°C to completely remove the water. After the waste liquid is stabilized, it enters the first tower body through the feed pipe for rectification. Control the relative vacuum degree of the first tower body to about -88KPa and the rectification temperature When the temperature is about 165°C, close the first valve a to form 100% reflux. After the rectification environment of the first tower body is stable, control the first valve to make 5%-6% ethylene glycol return to the first tower body. The ethylene glycol gas at the top...
Embodiment 3
[0038] Get 500ML waste liquid, detect by infrared analysis, diethylene glycol content is 20.12% in waste liquid, and ethylene glycol content is 52.34%, and 1.4BG (1.4 dibutyl alcohol) content is 25.32%, and surplus is a small amount of water and Polyester polyol.
[0039] Adopt embodiment one distillation system to separate the method for ethylene glycol, diethylene glycol in polyol waste liquid, have the following steps:
[0040] 1) Distill the waste liquid at 100°C to completely remove water. After the waste liquid is stabilized, it enters the first tower through the feed pipe for rectification. Control the relative vacuum of the first tower to about -89KPa, and the rectification temperature When the temperature is about 165°C, close the first valve a to form 100% reflux. After the rectification environment of the first tower body is stable, control the first valve to make 5%-6% ethylene glycol return to the first tower body. The ethylene glycol gas at the top of the first ...
PUM
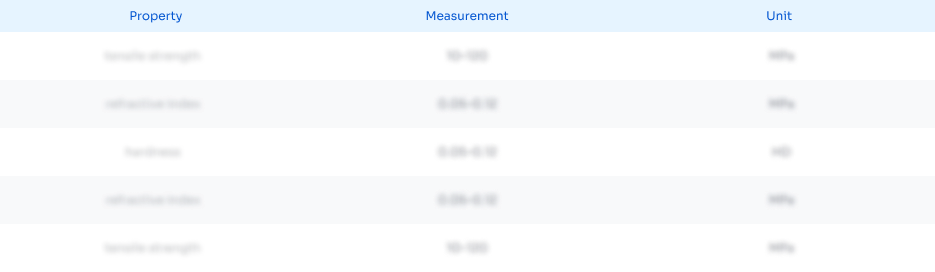
Abstract
Description
Claims
Application Information

- R&D Engineer
- R&D Manager
- IP Professional
- Industry Leading Data Capabilities
- Powerful AI technology
- Patent DNA Extraction
Browse by: Latest US Patents, China's latest patents, Technical Efficacy Thesaurus, Application Domain, Technology Topic, Popular Technical Reports.
© 2024 PatSnap. All rights reserved.Legal|Privacy policy|Modern Slavery Act Transparency Statement|Sitemap|About US| Contact US: help@patsnap.com