Double-sided printing method for plastic film
A plastic film and double-sided printing technology, applied in printing, printing post-processing, printing devices, etc., can solve the problems of poor surface ink adhesion, large registration error, easy to be damaged, etc., to ensure fastness, solve The effect of ink sticking back and avoiding ink sticking to each other
- Summary
- Abstract
- Description
- Claims
- Application Information
AI Technical Summary
Problems solved by technology
Method used
Image
Examples
specific Embodiment
[0036] refer to figure 2 Shown, for the specific embodiment of the plastic film double-sided printing method provided by the present invention, this method specifically comprises:
[0037] (1) Film unwinding: install the transparent printing film raw material to the unwinding reel, ready for printing;
[0038] (2) On-line corona: The transparent printing film raw material has only one treatment surface. Before printing on both sides, it is necessary to carry out online corona treatment on the first surface of the transparent printing film raw material to increase the surface tension of the film, which is conducive to improving the surface printing ink. Excellent adhesion; at the same time, the synchronization between corona and printing is guaranteed, and the stability of corona is guaranteed.
[0039] (3) Inner printing: carry out the inner printing process of inner printed graphics and texts;
[0040] (4) Anti-adhesive barrier treatment: Due to the effect of winding tensi...
PUM
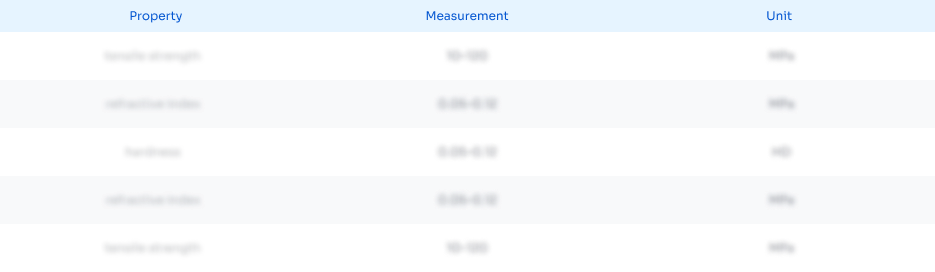
Abstract
Description
Claims
Application Information

- R&D
- Intellectual Property
- Life Sciences
- Materials
- Tech Scout
- Unparalleled Data Quality
- Higher Quality Content
- 60% Fewer Hallucinations
Browse by: Latest US Patents, China's latest patents, Technical Efficacy Thesaurus, Application Domain, Technology Topic, Popular Technical Reports.
© 2025 PatSnap. All rights reserved.Legal|Privacy policy|Modern Slavery Act Transparency Statement|Sitemap|About US| Contact US: help@patsnap.com