Method for regenerating waste gypsum model
A waste gypsum and model technology, applied in the field of gypsum, can solve the problems of long pouring time, shorten the initial and final setting time of gypsum powder, and low strength of gypsum powder, so as to improve the strength, prolong the initial and final setting time, and prolong the initial setting time Effect
- Summary
- Abstract
- Description
- Claims
- Application Information
AI Technical Summary
Problems solved by technology
Method used
Image
Examples
Embodiment 1
[0045] This embodiment provides a method for regenerating waste gypsum models. The collected waste gypsum models are smashed and sorted, and impurities and other non-gypsum items are removed first, and then the residue on the waste gypsum model is removed with a brush or a spatula. After crushing, pass the 60-mesh sieve to obtain coarse waste gypsum particles and transfer them to a stirring tank. Add water equivalent to 4 times the weight of the waste gypsum coarse particles and stir for 1.5 hours at 40°C. Centrifuge the filter while it is hot, discard the filtrate, add 4 times the mass of 10% hydrogen peroxide to the filter residue, stir for 1.5 hours, discard the filtrate after filtering, transfer the filter residue to the sedimentation tank, add water equivalent to 3 times the weight of the filter residue, and adjust the pH to 5.0. Let stand for 12 hours, remove the supernatant liquid, take the lower layer of sediment and place it in an autoclave, autoclave at a temperature o...
Embodiment 2
[0047] This embodiment provides a method for regenerating waste gypsum models. The collected waste gypsum models are smashed and sorted, and impurities and other non-gypsum items are removed first, and then the residue on the waste gypsum model is removed with a brush or a spatula. After crushing, pass 80 mesh sieve to obtain coarse waste gypsum particles and transfer them to a stirring tank. Add water equivalent to 5 times the weight of waste gypsum coarse particles and stir at 55°C for 1.0 hour. Centrifuge the filter while it is hot, discard the filtrate, add 5 times the mass of 10% hydrogen peroxide to the filter residue, stir for 2 hours, discard the filtrate after filtration, transfer the filter residue to the sedimentation tank, add water equivalent to 2 times the weight of the filter residue, and adjust the pH to 4. Let stand for 6 hours, remove the supernatant liquid, take the lower layer of sediment and place it in an autoclave, autoclave at a temperature of 120°C and a...
Embodiment 3
[0049] This embodiment provides a method for regenerating waste gypsum models. The collected waste gypsum models are smashed and sorted, and impurities and other non-gypsum items are removed first, and then the residue on the waste gypsum model is removed with a brush or a spatula. After crushing, pass the 60-mesh sieve to obtain coarse waste gypsum particles and transfer them to a stirring tank. Add water equivalent to 3 times the weight of the waste gypsum coarse particles and stir at 35°C for 2 hours. Centrifuge the filter while it is hot, discard the filtrate, add 4 times the weight of 5% hydrogen peroxide to the filter residue, stir for 1 hour, discard the filtrate after filtration, transfer the filter residue to the sedimentation tank, add water equivalent to 4 times the weight of the filter residue, and adjust the pH to 6. Let stand for 18 hours, remove the supernatant liquid, take the lower layer of sediment and place it in an autoclave, autoclave at a temperature of 130...
PUM
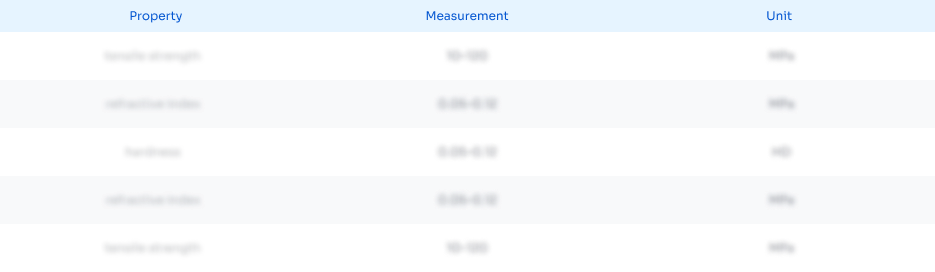
Abstract
Description
Claims
Application Information

- R&D
- Intellectual Property
- Life Sciences
- Materials
- Tech Scout
- Unparalleled Data Quality
- Higher Quality Content
- 60% Fewer Hallucinations
Browse by: Latest US Patents, China's latest patents, Technical Efficacy Thesaurus, Application Domain, Technology Topic, Popular Technical Reports.
© 2025 PatSnap. All rights reserved.Legal|Privacy policy|Modern Slavery Act Transparency Statement|Sitemap|About US| Contact US: help@patsnap.com