Residual oil desulfurization method as well as preparation method and production equipment of petroleum coke
A technology of petroleum coke and residual oil, applied in the petroleum industry, only multi-stage series refining and cracking process treatment, coke oven, etc., can solve the problems of flammability and explosion, high energy consumption, toxic organic solvents, etc., and achieve economical Significant benefits, simple process, continuous production effect
- Summary
- Abstract
- Description
- Claims
- Application Information
AI Technical Summary
Problems solved by technology
Method used
Image
Examples
preparation example Construction
[0057] On the other hand, the present invention provides a kind of preparation method of petroleum coke, comprises the following steps:
[0058] The desulfurized residual oil obtained according to the above residual oil desulfurization method is subjected to coking treatment to obtain petroleum coke.
[0059] The preparation method of petroleum coke provided by the present invention starts from the raw material of petroleum coke, and the raw material residue oil used is the residue oil with low sulfur content after pretreatment and electrostatic coalescence adsorption to remove sulfur-containing compounds. Petroleum coke with low sulfur content is prepared from the residual oil, which provides a new idea for the preparation of low sulfur petroleum coke. Compared with the reprocessing desulfurization of traditional high-sulfur petroleum coke, the preparation method significantly reduces energy consumption, has a simple process, is easy to operate, can realize continuous product...
Embodiment 1
[0065] This embodiment is a preparation method of petroleum coke, the process flow diagram is as follows figure 2 shown, including the following steps:
[0066] S1) Pretreatment: Residual oil and sodium hydroxide are mixed in a pretreatment tank at a mass ratio of 90:10 for reaction, the reaction temperature is 350°C, and the reaction time is 1.5h;
[0067] S2) Electrostatic adsorption: the residual oil after the pretreatment reaction is cooled to 300°C by heat exchange, and then enters an electrostatic treatment tank with a DC electric field strength of 5000V / cm for desulfurization treatment;
[0068] S3) Coking reaction: the residual oil after desulfurization treatment is heated up to 490° C. through heat exchange, and then enters the coke tower for coking reaction. The coking reaction time is 4 hours, and petroleum coke with low sulfur content is obtained after the reaction.
Embodiment 2
[0070] Present embodiment is a kind of preparation method of petroleum coke, comprises the following steps:
[0071] S1) Pretreatment: Residual oil and sodium hydroxide are mixed in a pretreatment tank at a mass ratio of 99:1 for reaction, the reaction temperature is 350°C, and the reaction time is 1.5h;
[0072] S2) Electrostatic adsorption: the residual oil after the pretreatment reaction is heated to 150°C and then enters an electrostatic treatment tank with a DC electric field strength of 1500V / cm for desulfurization treatment;
[0073] S3) Coking reaction: the residual oil after desulfurization treatment is heated up to 490° C. through heat exchange, and then enters the coke tower for coking reaction. The coking reaction time is 4 hours, and petroleum coke with low sulfur content is obtained after the reaction.
PUM
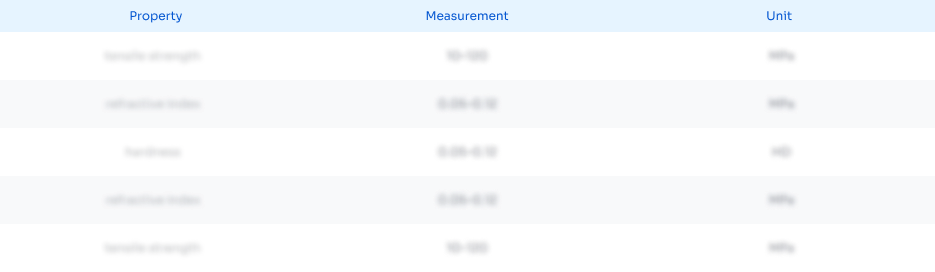
Abstract
Description
Claims
Application Information

- R&D Engineer
- R&D Manager
- IP Professional
- Industry Leading Data Capabilities
- Powerful AI technology
- Patent DNA Extraction
Browse by: Latest US Patents, China's latest patents, Technical Efficacy Thesaurus, Application Domain, Technology Topic, Popular Technical Reports.
© 2024 PatSnap. All rights reserved.Legal|Privacy policy|Modern Slavery Act Transparency Statement|Sitemap|About US| Contact US: help@patsnap.com