Production process of EPP (Expanded Polypropylene) foam plastics
A production process and technology of foam plastic, which is applied in the field of EPP foam plastic production technology, can solve the problems of foam plastic not adaptable, low hardness, cracking, etc., and achieve the effect of improving quality and high hardness
- Summary
- Abstract
- Description
- Claims
- Application Information
AI Technical Summary
Problems solved by technology
Method used
Examples
Embodiment
[0033] A kind of production technique of EPP foam plastic, comprises the steps:
[0034] 1) Initial expansion: Use water vapor to heat the EPP foam plastic raw material to achieve the effect of initial expansion. The heating temperature is 65°C and the heating time is 25 minutes;
[0035] 2), press material:
[0036] a), pre-compression: apply 0.7 kg of pressure to the first expanded EPP foam, and the compression time is 25 minutes;
[0037] b) The first pressurization: After the pre-pressing is finished, apply a pressure of 3 kg to the EPP foam, and the pressing time is 500 minutes;
[0038] c), the first pressure release: after the first pressurization is completed, apply 2 kg of pressure to the EPP foam, and the pressing time is 100 minutes;
[0039] d), the first flip: after the first pressure release, flip the upper and lower faces of the EPP foam and turn it over for 30 minutes;
[0040] e), the second pressurization: after the first flip, apply 6 kg of pressure to th...
PUM
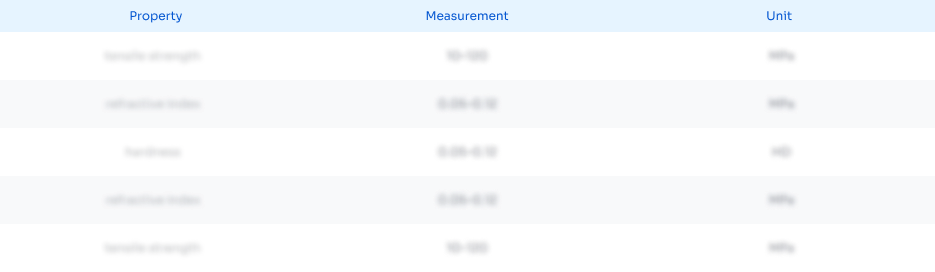
Abstract
Description
Claims
Application Information

- R&D Engineer
- R&D Manager
- IP Professional
- Industry Leading Data Capabilities
- Powerful AI technology
- Patent DNA Extraction
Browse by: Latest US Patents, China's latest patents, Technical Efficacy Thesaurus, Application Domain, Technology Topic, Popular Technical Reports.
© 2024 PatSnap. All rights reserved.Legal|Privacy policy|Modern Slavery Act Transparency Statement|Sitemap|About US| Contact US: help@patsnap.com