A modeling method of three-dimensional finite element model
A modeling method and finite element technology, applied in the modeling field of 3D finite element model, can solve the problem of unguaranteed mesh quality, and achieve the effect of saving modeling time, improving mesh quality, and ensuring mesh quality.
- Summary
- Abstract
- Description
- Claims
- Application Information
AI Technical Summary
Problems solved by technology
Method used
Image
Examples
Embodiment 1
[0040] Taking the electromagnetic railgun as an example, the schematic diagram of the double-layer electromagnetic railgun is as follows figure 1 As shown, the three-dimensional entity of the double-layer electromagnetic railgun includes two upper rails 1, two lower rails 2, an upper armature 3, and a lower armature 4, wherein the rails are made of copper and the armature is made of aluminum. In this object entity, the upper guide rail 1 and the lower guide rail 2 have a plane symmetrical structure, and the long side direction is zThe axial direction is the axial direction of plane symmetry, and the upper layer armature 3 and the lower layer armature 4 are located in different positions due to different speeds of movement. In this calculation example, it is assumed that the vertical position of the upper layer armature is in the front, and the lower layer armature is behind, and The positions of the two overlap partially in the vertical direction. In addition, in the finite e...
Embodiment 2
[0047] The cable tunnel in the project is shown as Figure 11 As shown, the structural characteristics of the entity object are: power cables with different voltage levels and different arrangements; and cable line supports, as well as tunnel concrete walls and air in the tunnel. Along the cable and tunnel extension direction is z axis, where the power cables and tunnel walls and the air area are z The planar symmetric structure in the axial direction, but there is one support at a certain distance, which is not a planar symmetric structure. Take the cable tunnel as an example to describe the implementation process:
[0048] (1): Establish two-dimensional models of power cable sections, brackets, tunnel walls, and air areas with different voltage levels and different arrangements, such as Figure 12 shown.
[0049] (2): Divide the two-dimensional model into finite elements using triangular meshes, such as Figure 13 As shown, a two-dimensional finite element model is gene...
PUM
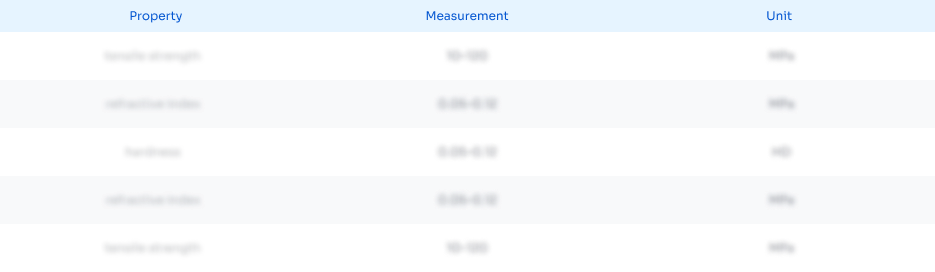
Abstract
Description
Claims
Application Information

- R&D Engineer
- R&D Manager
- IP Professional
- Industry Leading Data Capabilities
- Powerful AI technology
- Patent DNA Extraction
Browse by: Latest US Patents, China's latest patents, Technical Efficacy Thesaurus, Application Domain, Technology Topic, Popular Technical Reports.
© 2024 PatSnap. All rights reserved.Legal|Privacy policy|Modern Slavery Act Transparency Statement|Sitemap|About US| Contact US: help@patsnap.com