Continuous polyester fabric padding and dyeing method free of boiling and washing process and polyester fabric
A polyester fabric, non-cooking technology, applied in the dyeing method, textiles and papermaking, etc., can solve the problems of large wastewater discharge, large water consumption, high energy consumption, etc., and achieve the goal of improving economic benefits, reducing production costs, and shortening the process flow Effect
- Summary
- Abstract
- Description
- Claims
- Application Information
AI Technical Summary
Problems solved by technology
Method used
Examples
Embodiment 1
[0019] The dyed fabric is 75D polyester jersey, with a weight of 120 grams per square meter (120g / m 2 ), stained orange.
[0020] Step 1: Preparation of dyeing working solution
[0021] Add 100KG of soft water to the 500KG dyeing solution batching tank, start stirring, add 1.5KG of water-absorbing resin sodium acrylate acrylamide copolymer, after fully dissolving, add 0.25KG of polyester repair agent, 1KG of sodium dodecylbenzenesulfonate, Urea 2KG, stir well, add 200KG water, stir for 30 minutes, add disperse dye 3R 2KG, stir well, add polydimethyldiallylammonium chloride color fixing agent 5KG, add the remaining water , continue to stir for 30 minutes, open the dye liquid delivery valve, pass the dyeing working solution in the batching tank through the delivery pipeline, and quantitatively filter it into the batching tank next to the machine for use.
[0022] Step 2: Pad Dyeing of Polyester Fabric
[0023] Open the infusion delivery valve of the batching tank to deliver t...
Embodiment 2
[0029] The dyed fabric is 150D polyester twill jeanette with a weight of 120 grams per square meter (120g / m 2 ), stained red.
[0030] Step 1: Preparation of dyeing working solution
[0031] Add 100KG of soft water to the 500KG dyeing liquid batching tank, start stirring, add 2KG of water-absorbing resin potassium acrylate acrylamide copolymer, after fully dissolving, add 0.5KG of polyester repair agent, 1.5KG of sodium dodecylbenzenesulfonate, Glycerol 2.5KG, after fully stirring evenly, add 200KG water, after stirring for 30 minutes, add disperse dye Ruby S-5BL 5KG, after fully stirring, add ammonium chloride modified dicyandiamide formaldehyde resin type color fixing agent 7.5KG, add the remaining water, continue to stir for 30 minutes, open the dye liquid delivery valve, pass the dyeing working solution in the batching tank through the delivery pipeline, and quantitatively filter it into the batching tank next to the machine for use.
[0032] Step 2: Pad Dyeing of Polyes...
Embodiment 3
[0039] The dyed fabric is 300D polyester woven Oxford cloth with a weight of 280 grams per square meter (280g / m 2 ), stained orange.
[0040] Step 1: Preparation of dyeing working solution
[0041] Add 100KG of soft water to the 500KG dyeing solution batching tank, start stirring, add 1KG of water-absorbing resin sodium acrylate acrylamide copolymer, and after fully dissolving, add 1KG of polyester repair agent, 1KG of sodium laurate polyoxyethylene ether sulfate, ethylene glycol Alcohol 2KG, stir well, add 200KG water, stir for 30 minutes, add disperse dye ECT 300% 8KG, stir well, add polydimethyldiallylammonium chloride color fixing agent 10KG, add remaining Keep stirring for 30 minutes, open the dye liquid delivery valve, pass the dyeing working liquid in the batching tank through the delivery pipeline, and quantitatively filter it into the batching tank next to the machine for use.
[0042] Step 2: Pad Dyeing of Polyester Fabric
[0043] Open the infusion delivery valve...
PUM
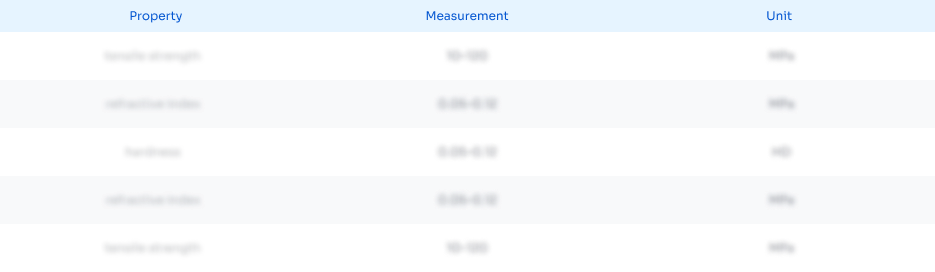
Abstract
Description
Claims
Application Information

- R&D
- Intellectual Property
- Life Sciences
- Materials
- Tech Scout
- Unparalleled Data Quality
- Higher Quality Content
- 60% Fewer Hallucinations
Browse by: Latest US Patents, China's latest patents, Technical Efficacy Thesaurus, Application Domain, Technology Topic, Popular Technical Reports.
© 2025 PatSnap. All rights reserved.Legal|Privacy policy|Modern Slavery Act Transparency Statement|Sitemap|About US| Contact US: help@patsnap.com