Method for using raw coal gas to assist material forming and material for iron and steel smelting
A technology of raw gas and materials, applied in the field of metallurgy, can solve problems such as energy waste
- Summary
- Abstract
- Description
- Claims
- Application Information
AI Technical Summary
Problems solved by technology
Method used
Image
Examples
Embodiment 1
[0036] This embodiment provides a method for using raw coal gas to assist material forming, which mainly includes the following steps:
[0037] The raw coal gas produced by the coke oven is introduced into the mixer containing the materials. The temperature of the raw gas before entering the mixer is 650°C. The water content of the material before mixing with raw coal gas is 0wt%. The main component of the material is iron ore concentrate (with some other impurities inevitably). Raw coal gas is introduced into the mixer through ordinary pipelines (non-insulated pipelines).
[0038] After the raw gas is mixed with the material, the raw gas is discharged from the mixer. The raw gas is mixed with the material to increase the temperature of the material and lower the temperature of the raw gas. The net gas volume that can be produced per 1 ton of material is 250m 3 The barren gas mixture.
[0039] Among them, please refer to figure 1 , figure 1 A schematic diagram of the s...
Embodiment 2
[0042] This embodiment provides a method for using raw coal gas to assist material forming, which mainly includes the following steps:
[0043] The raw coal gas produced by the coke oven is introduced into the mixer containing the materials. The temperature of raw coal gas before entering the mixer is 850°C. The water content of the material before mixing with raw coal gas is 6.5wt%. The main components of the material are iron concentrate, iron and steel plant dust (with some other impurities inevitably). Raw coal gas is introduced into the mixer through the insulation pipe. The thermal insulation pipeline is provided with a gate valve for controlling whether the thermal insulation pipeline is connected to the mixer.
[0044] After the raw gas is mixed with the material, the raw gas is discharged from the mixer. The raw gas is mixed with the material to increase the temperature of the material and lower the temperature of the raw gas. Every 1 ton of material can produce ...
Embodiment 3
[0048] This embodiment provides a method for using raw coal gas to assist material forming, which mainly includes the following steps:
[0049] The raw coal gas produced by the coke oven is introduced into the mixer containing the materials. The temperature of the raw gas before entering the mixer is 700°C. The water content of the material before mixing with raw coal gas is 2wt%. The main component of the material is a mixture of iron concentrate and coal powder (with some other impurities inevitably). Raw coal gas is introduced into the mixer through the insulation pipe. The thermal insulation pipeline is provided with a gate valve for controlling whether the thermal insulation pipeline is connected to the mixer.
[0050] After the raw gas is mixed with the material, the raw gas is discharged from the mixer. The raw gas is mixed with the material to increase the temperature of the material and lower the temperature of the raw gas. The net gas volume that can be produced...
PUM
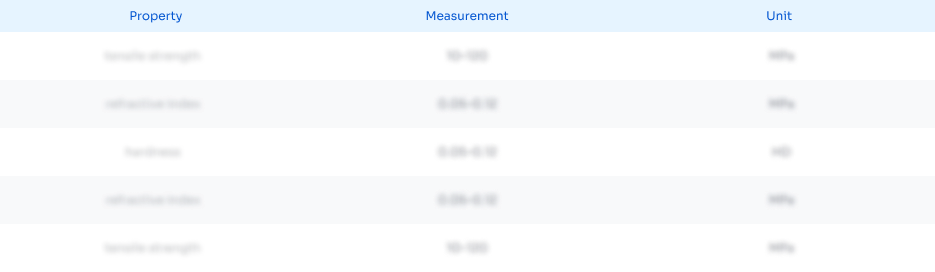
Abstract
Description
Claims
Application Information

- Generate Ideas
- Intellectual Property
- Life Sciences
- Materials
- Tech Scout
- Unparalleled Data Quality
- Higher Quality Content
- 60% Fewer Hallucinations
Browse by: Latest US Patents, China's latest patents, Technical Efficacy Thesaurus, Application Domain, Technology Topic, Popular Technical Reports.
© 2025 PatSnap. All rights reserved.Legal|Privacy policy|Modern Slavery Act Transparency Statement|Sitemap|About US| Contact US: help@patsnap.com