All-transfer elastic film and preparation method thereof
A technology of elastic film and PU resin, which is applied in the field of full-turn elastic film and its preparation, can solve the problems of large pollution, large loss, and low processing efficiency in the tanning process, and achieve increased production yield, reduced loss, and improved stability and efficiency
- Summary
- Abstract
- Description
- Claims
- Application Information
AI Technical Summary
Problems solved by technology
Method used
Image
Examples
Embodiment 1
[0026] A full-turn elastic membrane, comprising the following raw materials in parts by weight:
[0027]
[0028]
[0029] The solid content of the oily PU resin is 20%.
[0030] The preparation method of the oily PU resin is as follows: react 80 parts by weight of polyol, 30 parts by weight of polyisocyanate, and 0.01 part by weight of catalyst at 70° C. for 2 hours, then add 5 parts by weight of polyol chain extender for chain extension reaction for 2 hours, Cool down to 30°C, add 5 parts by weight of triethylamine for neutralization reaction for 20 minutes; add organic solvent and stir evenly to obtain oily PU resin.
[0031] The polyol is a mixture composed of polycarbonate diol, polycaprolactone diol and polytetrahydrofuran diol in a weight ratio of 2:1:1, and the number average molecular weight of the polyol is 1000.
[0032] The polyisocyanate is composed of diphenylmethane diisocyanate, xylylene diisocyanate and methylcyclohexyl diisocyanate in a weight ratio of...
Embodiment 2
[0039] A full-turn elastic membrane, comprising the following raw materials in parts by weight:
[0040]
[0041] The solid content of the oily PU resin is 30%.
[0042] The preparation method of the oily PU resin is as follows: react 90 parts by weight of polyol, 35 parts by weight of polyisocyanate, and 0.02 parts by weight of catalyst at a temperature of 75° C. for 1.8 hours, then add 8 parts by weight of polyol chain extender for chain extension reaction 2.5 h, lower the temperature to 35°C, add 8 parts by weight of triethylamine to neutralize and react for 25 minutes; add an organic solvent and stir evenly to obtain an oily PU resin.
[0043] The polyol is a mixture composed of polycarbonate diol, polycaprolactone diol and polytetrahydrofuran diol in a weight ratio of 2.5:1.2:1, and the number average molecular weight of the polyol is 1500.
[0044] The polyisocyanate is composed of diphenylmethane diisocyanate, xylylene diisocyanate and methylcyclohexyl diisocyanate in...
Embodiment 3
[0051] A full-turn elastic membrane, comprising the following raw materials in parts by weight:
[0052]
[0053] The solid content of the oily PU resin is 35%.
[0054] The preparation method of the oily PU resin is as follows: react 100 parts by weight of polyol, 40 parts by weight of polyisocyanate, and 0.03 parts by weight of catalyst at 80°C for 1.5 hours, then add 10 parts by weight of polyol chain extender for chain extension reaction for 3 hours , lower the temperature to 40°C, add 10 parts by weight of triethylamine to neutralize and react for 30 minutes; add an organic solvent and stir evenly to obtain an oily PU resin.
[0055] The polyol is a mixture composed of polycarbonate diol, polycaprolactone diol and polytetrahydrofuran diol in a weight ratio of 3:1.5:1, and the number average molecular weight of the polyol is 2000.
[0056] The polyisocyanate is composed of diphenylmethane diisocyanate, xylylene diisocyanate and methylcyclohexyl diisocyanate in a weight...
PUM
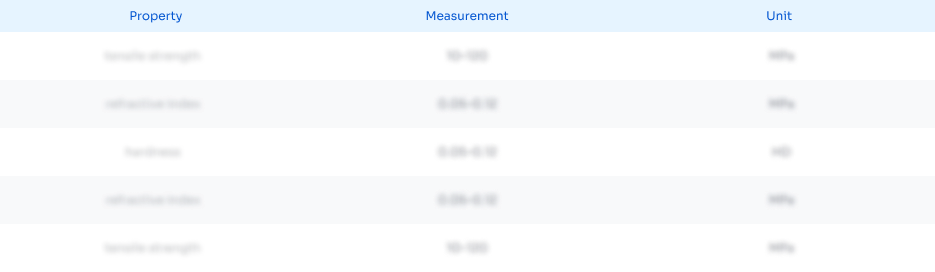
Abstract
Description
Claims
Application Information

- R&D Engineer
- R&D Manager
- IP Professional
- Industry Leading Data Capabilities
- Powerful AI technology
- Patent DNA Extraction
Browse by: Latest US Patents, China's latest patents, Technical Efficacy Thesaurus, Application Domain, Technology Topic, Popular Technical Reports.
© 2024 PatSnap. All rights reserved.Legal|Privacy policy|Modern Slavery Act Transparency Statement|Sitemap|About US| Contact US: help@patsnap.com