Dynamic design method of high-speed double-rolling bearing electric spindle rotor system
A rolling bearing and system dynamic technology, applied in computer-aided design, design optimization/simulation, calculation, etc., can solve the problem of not being able to obtain the corresponding relationship between the dynamic characteristics of the rotor system of the electric spindle and the bearing configuration mode, reducing the accuracy of the dynamic design of the electric spindle, and inability to Objectively reflect the dynamic behavior of high-speed motorized spindle rotors and other issues
- Summary
- Abstract
- Description
- Claims
- Application Information
AI Technical Summary
Problems solved by technology
Method used
Image
Examples
Embodiment Construction
[0123] The method for dynamic design of the rotor system of the high-speed double rolling bearing electric spindle of the present invention will be further described in detail below in conjunction with an embodiment (51000rpm high-speed grinding electric spindle).
[0124] figure 1 The specific content of the dynamic design method of the high-speed double rolling bearing electric spindle rotor system of the present invention is given, including the following steps:
[0125] Step 1: According to the use requirements of the electric spindle: the working speed is 51000rpm, the static stiffness of the shaft end is greater than 10N / μm, complete the structural configuration design of the high-speed double rolling bearing electric spindle rotor system, such as figure 2 As shown: the main shaft rotor 3 is supported on two sets of double-connected rolling bearings, and the front bearing 2 and the rear bearing 6 are arranged in series. The motor rotor 4 is installed on the main shaft ...
PUM
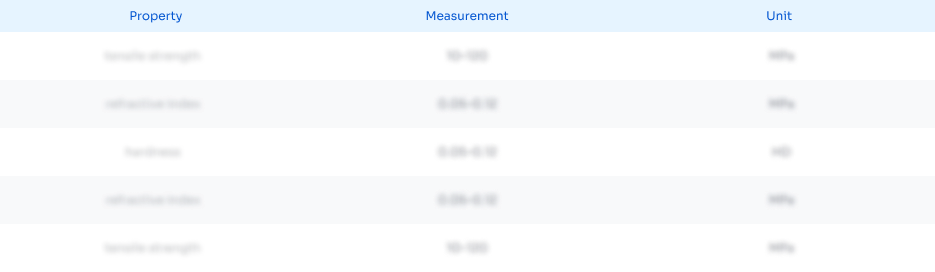
Abstract
Description
Claims
Application Information

- R&D
- Intellectual Property
- Life Sciences
- Materials
- Tech Scout
- Unparalleled Data Quality
- Higher Quality Content
- 60% Fewer Hallucinations
Browse by: Latest US Patents, China's latest patents, Technical Efficacy Thesaurus, Application Domain, Technology Topic, Popular Technical Reports.
© 2025 PatSnap. All rights reserved.Legal|Privacy policy|Modern Slavery Act Transparency Statement|Sitemap|About US| Contact US: help@patsnap.com