A method for modeling rigidity of a transmission chain of a double-screw drive system
A technology of driving system and modeling method, applied in the field of dynamics, which can solve the problems of finite element method relying on mesh accuracy calculation efficiency, increasing calculation error, ignoring joint surface stiffness and damping, etc.
- Summary
- Abstract
- Description
- Claims
- Application Information
AI Technical Summary
Problems solved by technology
Method used
Image
Examples
Embodiment Construction
[0066] In order to make the object, technical solution and advantages of the present invention clearer, the present invention will be further described in detail below in conjunction with the accompanying drawings and embodiments.
[0067] This example relies on the self-developed double-screw-driven workbench system, such as figure 2 shown.
[0068] A modeling method for the stiffness of the transmission chain of a double-screw drive system, such as figure 1 shown, including the following steps:
[0069] Step1, calculate the contact stiffness of the rolling contact surface. The rolling joint surface includes the screw-nut joint surface and the bearing joint surface. It is assumed that the contacting rolling elements between the contact surfaces obey the Hertz contact theory, and the mutual contacting rolling elements between the joint surfaces are regarded as elastic bodies, as long as Knowing the parameters between the contact rolling elements, the contact stiffness bet...
PUM
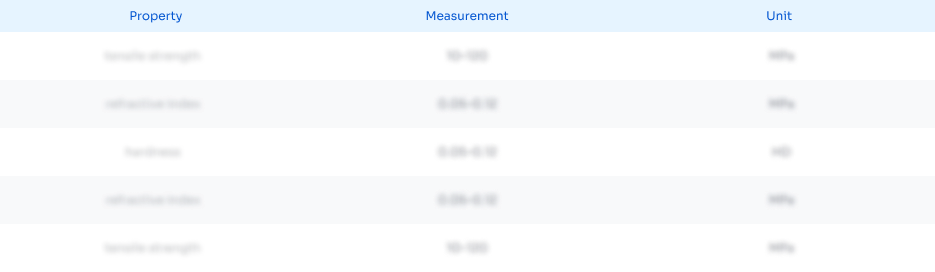
Abstract
Description
Claims
Application Information

- R&D
- Intellectual Property
- Life Sciences
- Materials
- Tech Scout
- Unparalleled Data Quality
- Higher Quality Content
- 60% Fewer Hallucinations
Browse by: Latest US Patents, China's latest patents, Technical Efficacy Thesaurus, Application Domain, Technology Topic, Popular Technical Reports.
© 2025 PatSnap. All rights reserved.Legal|Privacy policy|Modern Slavery Act Transparency Statement|Sitemap|About US| Contact US: help@patsnap.com