Cold-drawing inner mold for eliminating inner spiral ribbing of steel pipe
A technology of internal spiral and internal mold, applied in the direction of wire drawing dies, etc., can solve problems such as difficult to eliminate, and achieve the effects of reducing extrusion stress, reducing drawing passes, and increasing length
- Summary
- Abstract
- Description
- Claims
- Application Information
AI Technical Summary
Problems solved by technology
Method used
Image
Examples
Embodiment Construction
[0012] Such as figure 1 , figure 2 and image 3 As shown, a cold-drawn inner mold for eliminating the inner spiral of the steel pipe for drawing a cold-drawn pipe with an aperture of φ125, it includes an inner mold body 1, and the outer surface of the inner mold body 1 is sequentially provided with first cones The wall-reducing section L1, the first cylindrical wall-reducing section L2, the transition section L3, the second conical wall-reducing section L4 and the second cylindrical wall-reducing section L5; the length of the first conical wall-reducing section L1 is 72mm, and the first conical wall-reducing section The cone angle α of the section L1 is 6 degrees; the diameter of the first cylindrical uniform wall section L2 is φ123mm, and the length is 20mm; the diameter of the transition section L3 is φ118.5mm, and the length is 3mm; the length of the second conical wall-reducing section L4 is 15mm, the cone angle β of the second cone wall-reducing section L4 is 12 degree...
PUM
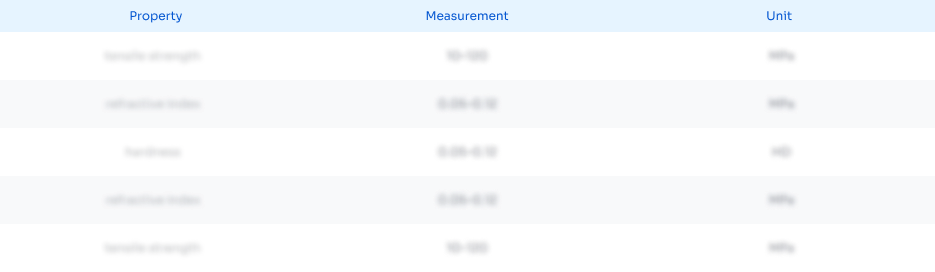
Abstract
Description
Claims
Application Information

- Generate Ideas
- Intellectual Property
- Life Sciences
- Materials
- Tech Scout
- Unparalleled Data Quality
- Higher Quality Content
- 60% Fewer Hallucinations
Browse by: Latest US Patents, China's latest patents, Technical Efficacy Thesaurus, Application Domain, Technology Topic, Popular Technical Reports.
© 2025 PatSnap. All rights reserved.Legal|Privacy policy|Modern Slavery Act Transparency Statement|Sitemap|About US| Contact US: help@patsnap.com