Reflector support and fixing method
A mirror support and fixing method technology, applied in installation, optics, instruments, etc., can solve the problems of forced displacement unloading ability and thermal deformation unloading ability, large flexibility of support structure, poor seismic performance, etc., to reduce dynamic response. Amplitude, reduced structural weight, good stability
- Summary
- Abstract
- Description
- Claims
- Application Information
AI Technical Summary
Problems solved by technology
Method used
Image
Examples
Embodiment Construction
[0043] The specific implementation manners of the present invention will be described in further detail below in conjunction with the accompanying drawings and specific embodiments.
[0044] see figure 1 As shown, the embodiment of the present invention provides a reflector support and fixing device for connecting the reflector 1 with the lens body frame, especially suitable for reflectors with a diameter not greater than 400mm. Such as figure 1 and 2 As shown, in the embodiment of the present invention, the reflector 1 is a circular reflector, and the upper and lower sides of the periphery are respectively provided with a circle of concave ring belts. The supporting and fixing device includes a support frame 2, three pressing blocks 3, six A film 5, three flexible bearings 4 and three groups of flexible bearing fixing components, such as image 3 and 4 As shown, the support frame 2 is an annular frame, and three flanges 21 are evenly distributed on the periphery along the...
PUM
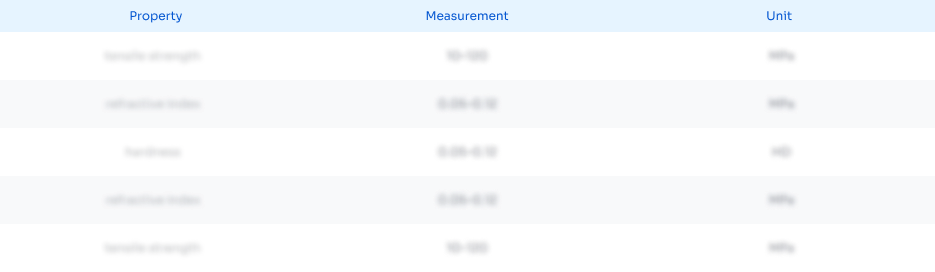
Abstract
Description
Claims
Application Information

- Generate Ideas
- Intellectual Property
- Life Sciences
- Materials
- Tech Scout
- Unparalleled Data Quality
- Higher Quality Content
- 60% Fewer Hallucinations
Browse by: Latest US Patents, China's latest patents, Technical Efficacy Thesaurus, Application Domain, Technology Topic, Popular Technical Reports.
© 2025 PatSnap. All rights reserved.Legal|Privacy policy|Modern Slavery Act Transparency Statement|Sitemap|About US| Contact US: help@patsnap.com