Impact and rubbing experiment device of rotating stator
An experimental device, the technology of rotating the stator, applied in the direction of measuring device, testing of mechanical components, testing of machine/structural components, etc., to achieve full-featured results
- Summary
- Abstract
- Description
- Claims
- Application Information
AI Technical Summary
Problems solved by technology
Method used
Image
Examples
Embodiment 1
[0038] The rubbing test device of the rotor stator provided by the present invention includes a box base, a box body, a three-way load cell, a displacement characteristic sensor, a strain gauge, a rubbing support mechanism, a leaf disc balance mechanism, a main shaft transmission mechanism and a gap adjustment mechanism, wherein the rubbing support mechanism is fixed on one side above the box base, the rubbing support mechanism is provided with a support ring, and the support ring is used as a stator, the main shaft transmission mechanism is fixed above the box body, and the main shaft transmission mechanism is connected to the leaf disk balance mechanism. And provide power for the blisk balance mechanism, the blisk of the blisk balance mechanism is used as the rotor, the stator and the rotor are arranged correspondingly, the rotor is placed in the middle of the stator, that is, the blisk is placed in the ring of the support ring. There is a casing on the inner wall of the supp...
Embodiment 2
[0064] Experimental device provided by the present invention carries out test process and can adopt following operation to carry out:
[0065] 1. Preparation before the test:
[0066] The experimental device should pre-adjust the rubbing gap to 0 before the experiment, and adjust the intrusion through the gap adjustment mechanism. The negative pole of the power supply is connected to the blade, and the positive pole of the power supply is connected to the casing. The current signal generates a current signal when it is in contact (generating an intrusion), so the gap is adjusted to 1 μm when the current is just generated through the gap adjustment mechanism, and the gap is considered to be 0.
[0067] 2. Friction characteristics at different speeds
[0068] For the rubbing characteristics at different speeds, it is necessary to control the remaining variables to remain unchanged. Set a given amount of rubbing, such as 50 μm, and drive the main shaft to rotate through the air ...
PUM
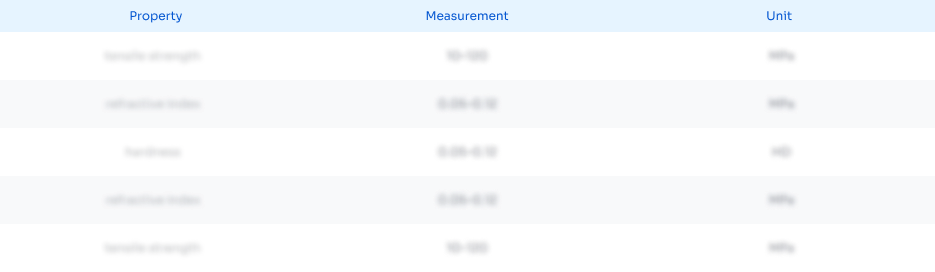
Abstract
Description
Claims
Application Information

- R&D Engineer
- R&D Manager
- IP Professional
- Industry Leading Data Capabilities
- Powerful AI technology
- Patent DNA Extraction
Browse by: Latest US Patents, China's latest patents, Technical Efficacy Thesaurus, Application Domain, Technology Topic, Popular Technical Reports.
© 2024 PatSnap. All rights reserved.Legal|Privacy policy|Modern Slavery Act Transparency Statement|Sitemap|About US| Contact US: help@patsnap.com