A kind of master alloy and its preparation method and application
An intermediate alloy and alloy technology, applied in the field of metallurgy, can solve problems such as difficult operation, high alloy impurity content, and inability to meet the requirements of high-temperature alloy smelting raw materials, so as to improve production efficiency, uniform alloying, and improve defects such as segregation and inclusions Effect
- Summary
- Abstract
- Description
- Claims
- Application Information
AI Technical Summary
Problems solved by technology
Method used
Image
Examples
Embodiment 1
[0045] Concrete preparation process is as follows:
[0046] (1) Furnace making - sintering: using Al 2 o 3 Make the furnace material to make the crucible, and sinter in the sintering furnace at 850°C for 3 hours;
[0047] (2) Ingredients: mainly Fe or Fe 2 o 3 , Cr or Cr 2 o 3 , MoO x , Nb 2 o 5 , Al as raw material;
[0048] (3) Mixing: Put the raw materials into the V-shaped mixer and mix evenly;
[0049] (4) Furnace loading: put the mixed raw materials into the sintered crucible;
[0050] (5) Reaction: Calcium peroxide (CaO 2 ), fine aluminum (Al) and magnesium powder (Mg) are uniformly mixed, wrapped in paper as an igniter and placed on the top of the raw material, and the ignition starts a spontaneous reaction;
[0051] (6) cooling: natural cooling in the air for 5 hours;
[0052] (7) Furnace removal-weighing: the crucible is disassembled, the alloy ingot is taken out therefrom, and weighed;
[0053] (8) Finishing: use a grinder to remove the slag layer and ...
Embodiment 2~8
[0057] According to the method operation of embodiment 1, difference with embodiment 1 is: embodiment 2 adds K 2 Cr 2 o 7 To improve the heat of the overall reaction, the reaction is fully carried out; Embodiment 3~5 except using K 2 Cr 2 o 7 In addition to increasing the heat of reaction, part of Mg was used to replace Al to reduce metal oxides to increase the yield of oxides; in addition, the expected value of the content of each element and the expected value of the yield of each metal oxide were adjusted when designing the formula. Embodiment 6~8 adds TiO 2 . The details of each reaction system are shown in Table 1, and the analysis results are shown in Table 2.
[0058] Table 1. FeAlCrMoNbTi alloy reaction system
[0059]
[0060] Table 2. The main component list (wt.%) of the multi-element alloy of embodiment
[0061]
[0062] The second step adopts the vacuum induction melting method: batching, furnace loading, exhaust, argon filling, smelting, refining, c...
Embodiment 9
[0064] Concrete preparation process is as follows:
[0065] (1) Ingredients: the primary alloy produced by the first step of aluminothermic reduction reaction is used as the raw material for the second step of smelting, and 2wt% LaCe mixed metal is added as a desulfurizer;
[0066] (2) Furnace loading: first put half of the iron-aluminum-chromium-molybdenum-niobium-titanium (FeAlCrMoNbTi) alloy into the crucible, then put the mixed metal of lanthanum and cerium into the crucible, and finally put the rest of the alloy into the crucible;
[0067] (3) Exhaust: evacuate the vacuum induction furnace to 7.8 Pa, and use a small power of 5kw to bake the crucible to remove the attached gas;
[0068] (4) Argon filling-smelting: fill the vacuum induction furnace with argon to 10 kPa, slowly increase the power to 40kw to melt the alloy;
[0069] (5) Refining: Refining at 1700°C for 10 minutes, vacuuming again to remove the gas in the melt, and turning off the induction current after reac...
PUM
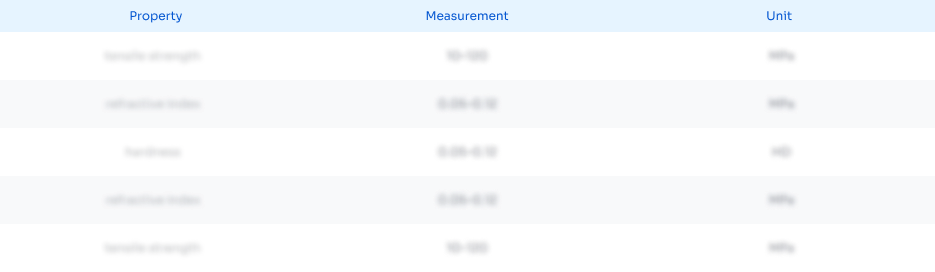
Abstract
Description
Claims
Application Information

- R&D
- Intellectual Property
- Life Sciences
- Materials
- Tech Scout
- Unparalleled Data Quality
- Higher Quality Content
- 60% Fewer Hallucinations
Browse by: Latest US Patents, China's latest patents, Technical Efficacy Thesaurus, Application Domain, Technology Topic, Popular Technical Reports.
© 2025 PatSnap. All rights reserved.Legal|Privacy policy|Modern Slavery Act Transparency Statement|Sitemap|About US| Contact US: help@patsnap.com