Preparation method of chlorophenoxycarboxylic acid
A technology of chlorophenoxy carboxylic acid and chlorophenoxy fatty alcohol, which is applied in the field of preparation of chlorophenoxy carboxylic acid, can solve the problems of high pressure in the treatment of three wastes, loss of active ingredients, poor chlorination selectivity, etc., and achieve improvement Product quality, avoiding effective costs, and improving the effect of chlorination selectivity
- Summary
- Abstract
- Description
- Claims
- Application Information
AI Technical Summary
Problems solved by technology
Method used
Image
Examples
Embodiment 1
[0050] Add 139.58g 99% phenoxyethanol (1mol), 0.21g 99% aluminum oxide and 1.19g 99% 2,4,5-tri-tert-butylisothiazole successively to a 500mL four-necked flask, and pass through at -20°C Inject 154.69g of 99% chlorine gas, complete the heat preservation reaction for 30min, distill at 1kpa pressure and collect fractions at 110-120°C to obtain 207.89g of 2,4-dichlorophenoxyethanol with a content of 99.1%. The yield is expressed as phenoxyethanol Ethanol 99.48%.
[0051] Add 18.71g of ZSM-5 molecular sieve to the distilled 2,4-dichlorophenoxyethanol as a catalyst, add 415.8g of water, feed 99.9% oxygen to a pressure of 0.7MPa, react at 130°C, and feed a total of 38.44g Oxygen, filter at 90°C after the reaction is completed, cool the filtrate to 15°C, filter to obtain 2,4-dichlorophenoxyacetic acid wet material, dry the wet material to obtain 221.71g of 2,4-dichlorophenoxyacetic acid, content 98.8% , the yield is 99.08% based on phenoxyethanol.
[0052] Utilize nuclear magnetic r...
Embodiment 2
[0060] Add 139.58g of 99% phenoxyethanol (1mol), 0.77g of 99% magnesium chloride and 0.35g of 99% 4,4'-dichlorophenylsulfide to a 500mL four-necked flask, and add 137.70 g of 99% sulfuryl chloride, after dripping and keeping warm for 30 minutes, distill at 1kpa pressure and collect fractions at 105-115°C to obtain 173.31g of 4-chlorophenoxyethanol, with a content of 98.8%, and a yield of 99.24% based on phenoxyethanol .
[0061] Add 10.40 g MoO to the distilled 4-chlorophenoxyethanol 3 As a catalyst, add 390.0g of water, feed 99.9% oxygen to a pressure of 0.1MPa, react at 80°C, feed a total of 36.84g of oxygen, filter at 80°C after the reaction is completed, cool the filtrate to 15°C, and filter to obtain 4-chloro The wet material of phenoxyacetic acid was dried to obtain 187.16 g of 4-chlorophenoxyacetic acid with a content of 98.5%, and the yield was 98.84% based on phenoxyethanol.
Embodiment 3
[0063] Add 167.92g 99% phenoxybutanol (1mol), 0.08g 99% zinc chloride and 1.26g 99% 3,4-dichlorothiophene successively in a 500mL four-necked flask, and feed 157.56 g 99% chlorine gas, heat preservation reaction for 30min, distill at 1kpa pressure and collect fractions at 120-130°C to obtain 236.06g of 2,4-dichlorophenoxybutanol with a content of 98.9%. Alcohol 99.34%.
[0064] Add 16.52g of activated carbon as a catalyst to the distilled 2,4-dichlorophenoxybutanol, add 236.1g of water, feed air to a pressure of 1.2MPa, and react at 60°C. A total of 220.95g of air is fed, and the reaction is completed in Filter at 95°C, cool the filtrate to 15°C, filter to obtain 2,4-dichlorophenoxybutyric acid wet material, dry the wet material to obtain 2,4-dichlorophenoxybutyric acid 249.85g, content 98.6%, yield 98.94% based on phenoxybutanol.
PUM
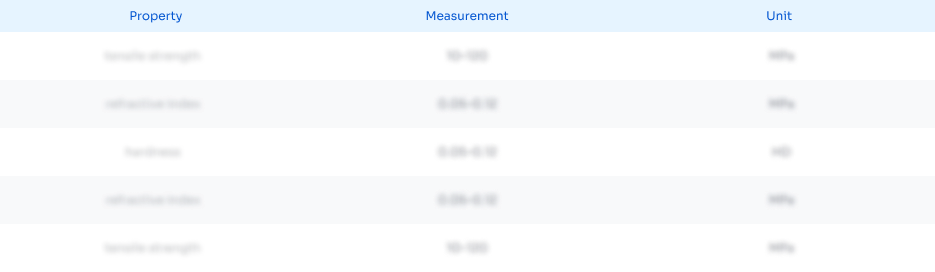
Abstract
Description
Claims
Application Information

- Generate Ideas
- Intellectual Property
- Life Sciences
- Materials
- Tech Scout
- Unparalleled Data Quality
- Higher Quality Content
- 60% Fewer Hallucinations
Browse by: Latest US Patents, China's latest patents, Technical Efficacy Thesaurus, Application Domain, Technology Topic, Popular Technical Reports.
© 2025 PatSnap. All rights reserved.Legal|Privacy policy|Modern Slavery Act Transparency Statement|Sitemap|About US| Contact US: help@patsnap.com