Prefabricating method for UHPC small box beam end diaphragm
A technology of small box girders and diaphragms, applied to bridges, manufacturing tools, bridge materials, etc., can solve the problems of large amount of construction work on site, unfavorable rapid construction, easy damage of horizontal connections, etc., and achieve the effect of improving prefabrication efficiency
- Summary
- Abstract
- Description
- Claims
- Application Information
AI Technical Summary
Problems solved by technology
Method used
Image
Examples
Embodiment Construction
[0023] refer to Figure 1 to Figure 3 , the prefabrication method of UHPC small box girder end diaphragm of the present invention, comprises the following steps:
[0024] S1. Prefabricate the box girder body consisting of top plate 10, bottom plate 20 and web 30 by pouring ultra-high performance concrete through the outer formwork and inner formwork, and the top plate 10, bottom plate 20 and web plate at the same cross-sectional position at the end of the box girder body 30 are respectively reserved with a top plate reserved hole 11, a bottom plate reserved hole 21 and a web reserved hole 31. The alignment between the top plate reserved hole 11 and the bottom plate reserved hole 21 is in the same vertical direction. The plate reserved holes 31 are also aligned in the same horizontal direction. The slow bonded prestressed tendons are pre-embedded in the bottom plate 20 and web 30 of the box girder body along the longitudinal direction, and the mid-span intervals are predetermin...
PUM
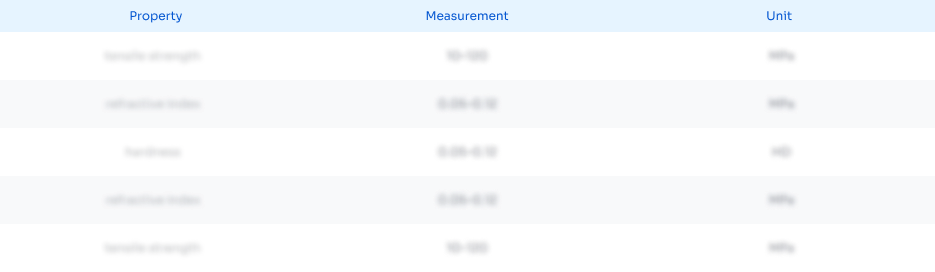
Abstract
Description
Claims
Application Information

- R&D
- Intellectual Property
- Life Sciences
- Materials
- Tech Scout
- Unparalleled Data Quality
- Higher Quality Content
- 60% Fewer Hallucinations
Browse by: Latest US Patents, China's latest patents, Technical Efficacy Thesaurus, Application Domain, Technology Topic, Popular Technical Reports.
© 2025 PatSnap. All rights reserved.Legal|Privacy policy|Modern Slavery Act Transparency Statement|Sitemap|About US| Contact US: help@patsnap.com