Side bar positioning multidimensional integrated leakage resisting chain feeding machine for achieving feeding machine conveyer side bar positioning multidimensional integrated leakage resisting method
A technology for side positioning and positioning strips, which is applied to conveyors, conveyor objects, conveyor control devices, etc., and can solve problems such as production stoppages, motor power overload, parallelograms, etc.
- Summary
- Abstract
- Description
- Claims
- Application Information
AI Technical Summary
Problems solved by technology
Method used
Image
Examples
Embodiment 1
[0112] Such as Figure 1 to Figure 4 As shown, the side bar positioning multi-dimensional integral leak-proof chain belt feeder 1 includes the frame 2 and the side bar positioning multi-dimensional integral leak-proof chain belt conveying device 3, etc., and the frame 2 supports the side bar positioning multi-dimensional integral leak-proof chain belt conveying device 3 Conveying materials, side strip positioning multi-dimensional integral leak-proof chain conveyor device 3 includes buckle chain multi-dimensional integral leak-proof side positioning strip 4, side positioning strip 5, buckle side positioning strip ring chain 6, chain belt locking piece 7, chain The gear driving part 8 and the sprocket redirecting part 9, etc., the buckle chain multi-dimensional integral leak-proof side positioning strip 4 includes the perforated buckle chain multi-dimensional integral leak-proof side positioning strip 10, etc., the buckle chain multi-dimensional integral leak-proof side position...
Embodiment 2
[0115] Such as Figure 5 to Figure 6 As shown, the buckle chain multi-dimensional overall leak-proof side positioning strip 4 includes an integrated buckle chain multi-dimensional overall leak-proof side positioning strip 13, etc. The side positioning strip 5 on the side of the buckle chain multi-dimensional integral leak-proof side positioning strip 13 is fastened on the ring chain of the buckle side positioning strip, and the sprocket drive part drives the integrated buckle chain multi-dimensional integral leak-proof side positioning strip 13 to transport materials forward .
[0116] Others are with embodiment 1.
Embodiment 3
[0118] Such as Figure 7 to Figure 9As shown, the buckle chain multi-dimensional overall leak-stopping side positioning strip includes the buckle chain that can be folded into an annular belt multi-dimensional integral leak-stopping side positioning strip 14, etc. Use the side positioning strip 5 to buckle on the buckle side positioning strip ring chain 6, and the buckle chain can be folded into a ring belt. Belt 15, multi-dimensional overall leak-proof side positioning strip Long belt ring-shaped sealing chain Belt 15 is buckled on the sprocket driving part and the sprocket redirecting part, driven by the sprocket driving part for continuous feeding, buckle chain Multi-dimensional integral leak-proof side positioning bar The outer surface of the belt is an integral surface without leaks to ensure no leakage, no sticking, no scraping of belt materials, etc. The side positioning strip 5 buckles the multi-dimensional overall leak-proof side positioning strip 4 of the buckle chai...
PUM
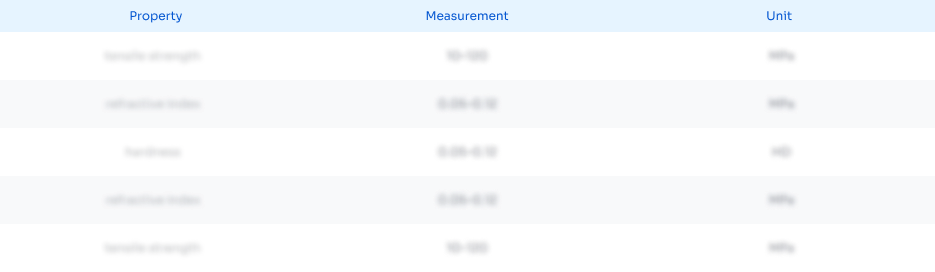
Abstract
Description
Claims
Application Information

- R&D
- Intellectual Property
- Life Sciences
- Materials
- Tech Scout
- Unparalleled Data Quality
- Higher Quality Content
- 60% Fewer Hallucinations
Browse by: Latest US Patents, China's latest patents, Technical Efficacy Thesaurus, Application Domain, Technology Topic, Popular Technical Reports.
© 2025 PatSnap. All rights reserved.Legal|Privacy policy|Modern Slavery Act Transparency Statement|Sitemap|About US| Contact US: help@patsnap.com