Continuous flowing preparation system and method
A preparation system and controller technology, applied in the fields of materials, chemical industry, and chemistry, can solve the problems of limited heat transfer rate, unsuitable for large flow continuous flow preparation, etc., to improve heat transfer efficiency, rapid heating, and increase heat transfer rate Effect
- Summary
- Abstract
- Description
- Claims
- Application Information
AI Technical Summary
Problems solved by technology
Method used
Image
Examples
Embodiment 1
[0047] Embodiment 1-continuous flow preparation system
[0048] refer to Figure 1 to Figure 3 As shown, the continuous flow preparation system of the present invention includes a controller and sequentially connected sampling channels, reactors and sampling channels; the reaction solution flows into the tubular reactor from the sampling channel, and then flows out of the product from the sampling channel;
[0049] refer to Figure 4 to Figure 12 , the reactor of the present invention is a tubular reactor, including a conductive reaction tube and a power module; the power module includes a power output terminal and a control terminal, and the power output terminal is electrically connected to the two ends of the reaction tube; the reaction tube is provided with a temperature Sensor, the temperature sensor detects the temperature signal in the reactor and transmits it to the controller. The controller controls the output voltage of the power module through the control terminal...
Embodiment 1-1
[0052] Based on Example 1, refer to Figure 1 to Figure 3 , There are one or more sampling channels, the sampling channel is provided with a sampling valve and a sampling pump, the controller controls the opening or closing of the sampling valve, and the start, pump speed and shutdown of the sampling pump. The sampling valve and the sampling pump can adopt existing metering valves and metering pumps. The controller can be realized by using existing computer, industrial computer or microcontroller. By controlling the flow rate of each sampling pump, the flow and ratio of different reactants can be flexibly adjusted.
[0053] Such as image 3 , when there are multiple sampling channels, the sampling outlets of the multiple sampling channels are connected to the sampling ports of the tubular reactor through the mixer. The mixer is used to mix the reactants pumped in from multiple sampling channels, and then enter the tubular reactor, and the mixer can adopt the existing T-type...
Embodiment 1-2
[0064] The difference between this embodiment and embodiment 1-1 is:
[0065] refer to Figure 5 , Figure 8 , Figure 9 with Figure 11 As shown, the reaction tube of the tubular reactor is a serpentine tube (S-shaped tube). Under the same length of the reaction tube, the floor area of the reactor can be effectively reduced compared with the linear tubular reactor.
PUM
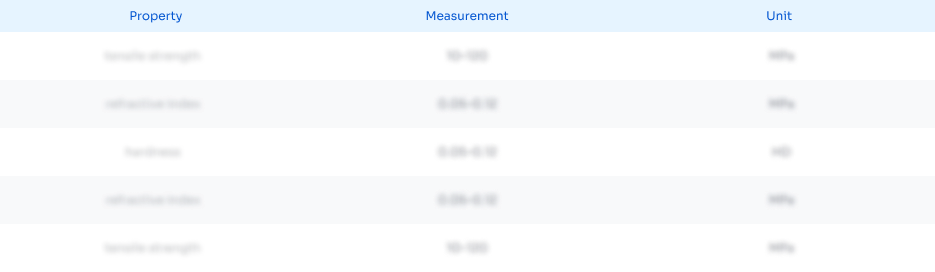
Abstract
Description
Claims
Application Information

- R&D
- Intellectual Property
- Life Sciences
- Materials
- Tech Scout
- Unparalleled Data Quality
- Higher Quality Content
- 60% Fewer Hallucinations
Browse by: Latest US Patents, China's latest patents, Technical Efficacy Thesaurus, Application Domain, Technology Topic, Popular Technical Reports.
© 2025 PatSnap. All rights reserved.Legal|Privacy policy|Modern Slavery Act Transparency Statement|Sitemap|About US| Contact US: help@patsnap.com