Central shaft torque detection system
A detection system and shaft torque technology, applied in force/torque/work measuring instruments, mechanical bearing testing, fluid pressure measurement involving magnet displacement, etc., can solve the problem of poor durability and the inability to respond accurately and timely to the shaft torque , short sensor life and other issues, to achieve the effect of improving riding comfort, improving man-machine synchronization, and accurate torque
- Summary
- Abstract
- Description
- Claims
- Application Information
AI Technical Summary
Problems solved by technology
Method used
Image
Examples
Embodiment 1
[0057] Embodiment 1 is basically as attached figure 1 As shown: the central shaft 1 torque detection system includes a lock nut 2, a claw 3, a left headset 22, a right headset 4, a central shaft 1, a deformation bridge 6, a sleeve and a magnetic isolation sleeve 10.
[0058] Such as figure 1 As shown in and , the left end and the right end of the central axis 1 are respectively connected to the left crank of the left pedal and the right crank of the right pedal by fastening screws, the left crank is located on the left side of the left headset 22, and the right crank is located on the right headset 4 to the right. An external thread is formed on the outer surface of the central axis 1 at the position connected to the deformation bridge 6 . The deformable bridge 6 is sleeved on the central shaft 1, and the deformable bridge 6 and the central shaft 1 are connected by reverse threads, and the threaded part of the central shaft 1 is locked with the internal thread of the deforma...
Embodiment 2
[0112] Such as Figure 6 As shown, the difference between this embodiment and Embodiment 1 is that the double Hall assembly and the bipolar linear Hall 26 are connected in the torque acquisition circuit, and the first micro-controller obtains the characteristic pedaling frequency and the centering frequency from the double Hall assembly. For the electrical signal of the rotation direction of the shaft 1, the first microcontroller obtains the electrical signal representing the crank rotation angle from the bipolar linear Hall 26, and transmits these electrical signals to the torque processing control circuit. At this time, the two circuits can be arranged together on the central axis 1 or separately, the torque acquisition circuit is arranged on the central axis 1 and the torque processing control circuit is arranged on the mounting sleeve 9 . When the torque acquisition circuit and the torque processing control circuit are set separately, the first transmitting module and the ...
Embodiment 3
[0114] Such as Figure 7 As shown, the difference between this embodiment and Embodiment 1 is that the double Hall assembly and the strain gauge 12 units are connected in the torque acquisition circuit, and the first micro-controller obtains the characteristic pedaling frequency and the rotation of the central shaft 1 from the double Hall assembly. As for the electrical signal of the direction, the bipolar linear Hall 26 is connected in the torque processing control circuit, and the second micro-controller obtains an electrical signal representing the rotation angle of the crank from the bipolar linear Hall 26. At this time, the two circuits can be arranged together on the central axis 1 or separately, the torque acquisition circuit is arranged on the central axis 1 and the torque processing control circuit is arranged on the mounting sleeve 9 . When the torque acquisition circuit and the torque processing control circuit are set separately, the first transmitting module and t...
PUM
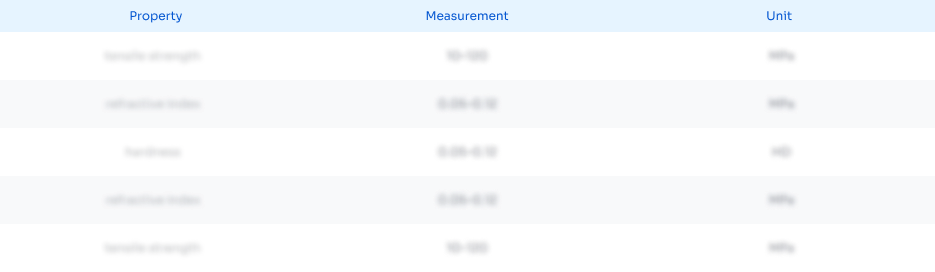
Abstract
Description
Claims
Application Information

- R&D
- Intellectual Property
- Life Sciences
- Materials
- Tech Scout
- Unparalleled Data Quality
- Higher Quality Content
- 60% Fewer Hallucinations
Browse by: Latest US Patents, China's latest patents, Technical Efficacy Thesaurus, Application Domain, Technology Topic, Popular Technical Reports.
© 2025 PatSnap. All rights reserved.Legal|Privacy policy|Modern Slavery Act Transparency Statement|Sitemap|About US| Contact US: help@patsnap.com