Non-contact three-dimensional automatic scanning testing system
A non-contact, scanning test technology, applied in general control systems, control/adjustment systems, measuring devices, etc., can solve the problems of slow movement and measurement speed, can only be used in laboratories, and cannot measure workpieces, etc., to improve Effects of measurement efficiency, improvement of measurement accuracy, and expansion of measurement range
- Summary
- Abstract
- Description
- Claims
- Application Information
AI Technical Summary
Problems solved by technology
Method used
Image
Examples
Embodiment Construction
[0018] The following will clearly and completely describe the technical solutions in specific embodiments of the present invention in conjunction with the schematic structural diagrams of the present invention. Apparently, the described embodiments are only some of the embodiments of the present invention, but not all of them. Based on the embodiments of the present invention, all other embodiments obtained by persons of ordinary skill in the art without making creative efforts belong to the protection scope of the present invention.
[0019] The non-contact three-dimensional automatic scanning test system includes a positioner 1, a gantry support 2, a robot 3, a measuring workpiece 4, and a data processing control system 5. The positioner 1 includes two support brackets 12 and a rotating clamping device 11. The support bracket 12 is provided with a motor and a gear inside, and the end of the support bracket 12 is provided with a rotating clamping device 11, and the measuring ...
PUM
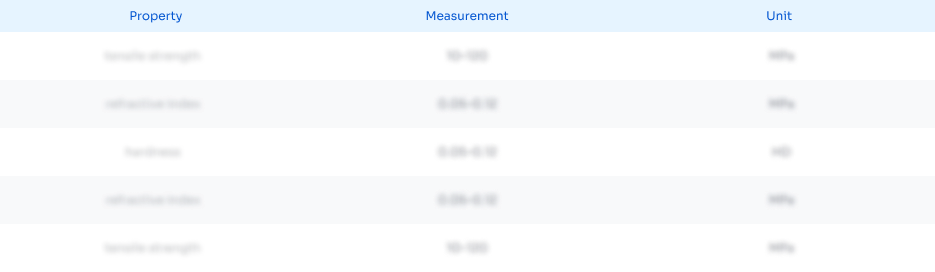
Abstract
Description
Claims
Application Information

- R&D
- Intellectual Property
- Life Sciences
- Materials
- Tech Scout
- Unparalleled Data Quality
- Higher Quality Content
- 60% Fewer Hallucinations
Browse by: Latest US Patents, China's latest patents, Technical Efficacy Thesaurus, Application Domain, Technology Topic, Popular Technical Reports.
© 2025 PatSnap. All rights reserved.Legal|Privacy policy|Modern Slavery Act Transparency Statement|Sitemap|About US| Contact US: help@patsnap.com