A kind of production method and production system of bevel gear
A production method and technology for bevel gears, applied in the field of bevel gear production methods and production systems, can solve the problems of large surface roughness, general product accuracy, high energy consumption of presses, and achieve improved gear quality, convenient mold replacement, and mold life. long effect
- Summary
- Abstract
- Description
- Claims
- Application Information
AI Technical Summary
Problems solved by technology
Method used
Image
Examples
Embodiment 1
[0067] Embodiment 1 provides a kind of production method of bevel gear, and this method comprises the following steps:
[0068] (1) Prepare the material section that meets the requirements, usually using a predetermined size of round steel to cut to a predetermined length.
[0069] (2) Heat the material section to 1150-1180°C in the heating device (specifically, an intermediate frequency induction heating furnace).
[0070] (3) Grind the heated section into a material cake on the billet-making pendulum milling device (specifically, a 300T pendulum milling machine and corresponding moulds).
[0071] (4) In the middle part of the upper side of the cake, the central cone groove is rolled to a predetermined thickness by the billet making pendulum rolling device. The central cone groove is arranged vertically, and the upper opening is open.
[0072] (5) Punch out a through hole on the central cone groove through a punching device (specifically, a punching hydraulic press), and the...
Embodiment 2
[0088] Embodiment 2 provides a kind of production method of bevel gear, this comprises the following steps:
[0089] S101: Select materials according to the requirements of different types of products for material grades, and saw the material into sections according to the parameters of the process documents.
[0090] S102: heating the material section to a range of 1150°C to 1180°C in an induction heating furnace of an intermediate frequency furnace.
[0091] S103: Place the heated material section on the center of the lower mold of the 300T swing rolling machine, and roll the material section into a material cake through the upper mold plate.
[0092] S104: Without moving the cake, place a conical punch at the center of the cake to punch the center cone groove (in the design of the mold, considering the ease of forming the pit and the demoulding of the punch, a draft of about 10° is designed Taper, depth Considering the thinnest continuous skin, saving material and reducing...
Embodiment 3
[0101] Embodiment 3 provides a kind of bevel gear production system, see Figure 12 , The system includes a material section preparation device, a heating device, a billet swing milling device, a punching device, a ring expanding device, a forming swing milling device and a post-processing device, etc., which are arranged in sequence.
[0102] Wherein, the material section preparation device may specifically be a sawing machine.
[0103] Wherein, the heating device may specifically be a medium frequency induction heating furnace.
[0104] Among them, see Figure 7-9 The billet swing milling device includes a swing mill (300T) and a truncated cone-shaped punch 2 on it and an upper template 1 (circular) whose outer edge is turned downward. The punch 2 and the upper template 1 constitute the upper mold , the size of the upper template 1 corresponds to the product; the punch 2 and the upper template 1 are designed as a split structure, the taper of the punch 2 is 8-12°, and the ...
PUM
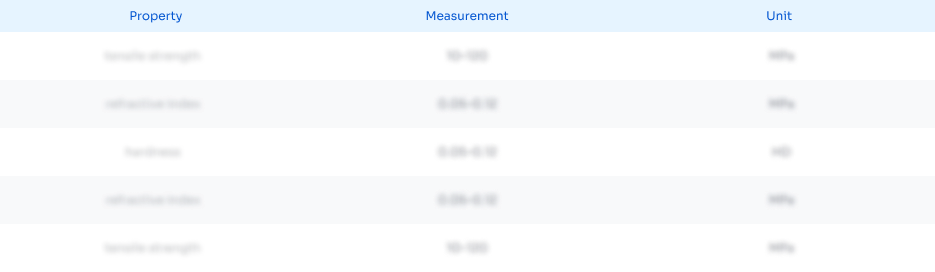
Abstract
Description
Claims
Application Information

- R&D
- Intellectual Property
- Life Sciences
- Materials
- Tech Scout
- Unparalleled Data Quality
- Higher Quality Content
- 60% Fewer Hallucinations
Browse by: Latest US Patents, China's latest patents, Technical Efficacy Thesaurus, Application Domain, Technology Topic, Popular Technical Reports.
© 2025 PatSnap. All rights reserved.Legal|Privacy policy|Modern Slavery Act Transparency Statement|Sitemap|About US| Contact US: help@patsnap.com