A Prediction Method of Point Contour Error on Part Side Milling Surface
A technology of contour error and prediction method, which is applied in the direction of program control, instrument, computer control, etc., and can solve the problems of inaccurate prediction results and less research
- Summary
- Abstract
- Description
- Claims
- Application Information
AI Technical Summary
Problems solved by technology
Method used
Image
Examples
Embodiment
[0115] Taking the XFYZBA structure machine tool to process an "S" shape with a wall thickness of 3mm as an example, the validity of the accuracy prediction algorithm is verified; the tool contact distribution of the local tool sweep surface is calculated, and part of the tool contacts 15 (along the tool axis Select 15 layers in the feed direction) × 20 (select 20 columns along the milling feed direction) = 300, the prediction results are as follows Figure 6 shown.
[0116] The result is as Figure 7 It can be seen from the figure that the predicted value has the same trend as the measured value, which verifies the validity of the prediction algorithm.
[0117] The present invention firstly calculates the ideal and actual tool contacts of side milling under multi-error conditions; then uses the method of surface fitting to obtain the parametric calculation models of the ideal and actual machining surfaces of the parts; according to the principle of contour error measurement, ...
PUM
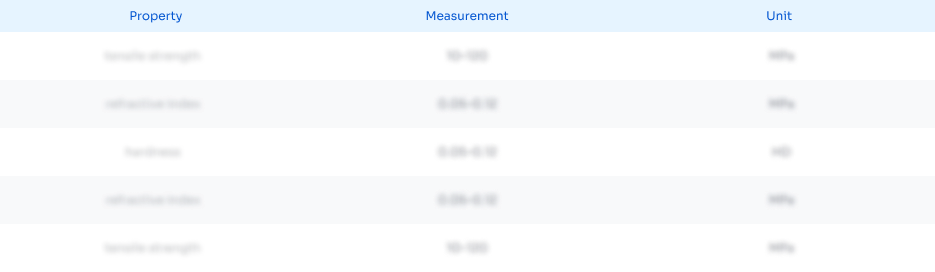
Abstract
Description
Claims
Application Information

- R&D
- Intellectual Property
- Life Sciences
- Materials
- Tech Scout
- Unparalleled Data Quality
- Higher Quality Content
- 60% Fewer Hallucinations
Browse by: Latest US Patents, China's latest patents, Technical Efficacy Thesaurus, Application Domain, Technology Topic, Popular Technical Reports.
© 2025 PatSnap. All rights reserved.Legal|Privacy policy|Modern Slavery Act Transparency Statement|Sitemap|About US| Contact US: help@patsnap.com