Dynamic load bearing design method applied to reciprocating compressor crankshaft
A technology of compressor crankshaft and design method, which is applied to crankshaft bearings, design optimization/simulation, special data processing applications, etc., can solve problems such as failure to meet bearing safety requirements, and achieve the effect of high safety
- Summary
- Abstract
- Description
- Claims
- Application Information
AI Technical Summary
Problems solved by technology
Method used
Image
Examples
Embodiment Construction
[0074] The present invention is described in further detail below in conjunction with accompanying drawing:
[0075] like figure 1 As shown, it is a dynamic load bearing design process. A dynamic load bearing design method applied to the crankshaft of a reciprocating compressor provided by the present invention includes the following steps:
[0076] 1. Determine the width-to-diameter ratio B / D according to the working conditions of the bearing (where B is the bearing width and D is the bearing diameter). For dynamic bearings, it is preferably 0.3 to 0.8. For bearings with complete circumferential grooves, it is usually preferred to choose the preferred range The upper limit (B / D=0.8), and the lower limit (B / D=0.3) for bearings without circumferential grooves and oil inlet holes;
[0077] 2. Refer to the diameter of the journal to determine the minimum radial clearance of the bearing, and the maximum value of the radial clearance of the bearing is 1.5 times the minimum value: ...
PUM
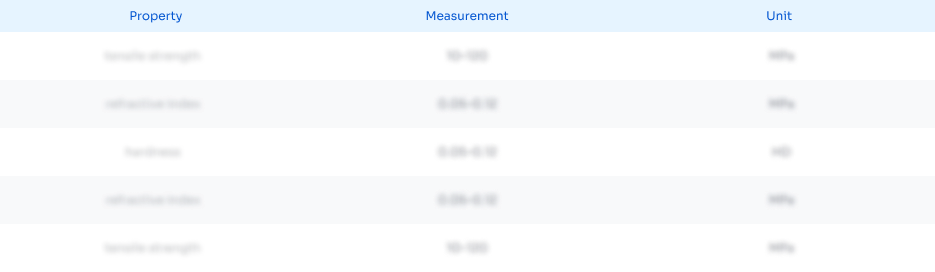
Abstract
Description
Claims
Application Information

- R&D
- Intellectual Property
- Life Sciences
- Materials
- Tech Scout
- Unparalleled Data Quality
- Higher Quality Content
- 60% Fewer Hallucinations
Browse by: Latest US Patents, China's latest patents, Technical Efficacy Thesaurus, Application Domain, Technology Topic, Popular Technical Reports.
© 2025 PatSnap. All rights reserved.Legal|Privacy policy|Modern Slavery Act Transparency Statement|Sitemap|About US| Contact US: help@patsnap.com