Catalyst loading method and coal catalytic gasification method
A catalyst and coal gasification technology, which is applied in gasification catalysts, production of combustible gas, petroleum industry, etc., can solve the problems of insufficient catalytic effect of catalysts, low gasification efficiency of gasification process, and low effective loading of catalysts, etc. To achieve the effect of increasing the effective load, improving the catalytic effect, and promoting dissociation
- Summary
- Abstract
- Description
- Claims
- Application Information
AI Technical Summary
Problems solved by technology
Method used
Image
Examples
Embodiment 1
[0058] The lignite of 40 mesh or more and the sodium carbonate of 200 mesh are mechanically mixed at a mass ratio of 10:1 and put into the reaction kettle, and water is added to the reactor at 5% of the mass of the coal to wet the surface of the coal particles and dissolve the catalyst. After the heat is released, after the temperature of the coal and the catalyst is lowered to room temperature, water of the same volume as the mixture of the coal and the catalyst is added to the reaction kettle. Heat up and increase pressure, react for 5h at a temperature of 200°C and a pressure of 2MPa, and then pass a mixture of oxygen and carbon dioxide (oxygen to dioxide ratio 1:1) into the reaction system, which controls the oxygen The molar ratio of total inflow to carbon in coal is 3:1, and the molar ratio in total inflow of carbon dioxide to carbon in coal is 2:1. The pH value of the mixed solution is 7.0 after the infusion time is 1h, and the reaction is stopped. The coal sample loaded...
Embodiment 2
[0060] The bituminous coal with a high degree of metamorphism above 80 mesh and potassium carbonate with 300 mesh are mechanically mixed with a mass ratio of 3:1 and put into the reactor, and 8% coal mass water is added to it to make the surface of the coal particles wet and dissolve The catalyst releases heat. After the temperature of the coal and the catalyst is lowered to room temperature, the volume of water added to the reactor is twice the volume of the mixture of the coal and the catalyst. Heat up and increase pressure, react for 2h at a temperature of 300°C and a pressure of 3MPa, and then introduce a mixture of oxygen, carbon dioxide and nitrogen (the ratio of oxygen, carbon dioxide and nitrogen is 1:1:1), and the oxygen is controlled The molar ratio of the total inflow of carbon dioxide to the carbon in the coal is 5:1, and the molar ratio of the total inflow of carbon dioxide to carbon in the coal is 4:1. After 2.5h, the PH value of the mixed solution is 8.0, and the ...
Embodiment 3
[0062] The sub-bituminous coal of 120 mesh or more and calcium oxide of 200 mesh are mechanically mixed with a mass ratio of 5:1 and then put into the reactor, and 7% of the coal mass is added to the reactor to make the surface of the coal particles wet and dissolve the catalyst to release heat After the temperature of the coal and the catalyst is lowered to room temperature, water with the same volume of the coal and the catalyst mixture is added to the reaction kettle. At the same time, sodium hydroxide with a mass of 15% coal is added to increase the alkalinity of the solution. Heating and increasing pressure, the temperature is 300 ℃, the pressure is 1.0 MPa conditions for 3 hours, and then a mixture of oxygen, carbon dioxide and nitrogen (oxygen, carbon dioxide and nitrogen ratio 1:2:2), which controls the oxygen The molar ratio of total input to carbon in coal is 4:1, the molar ratio of total carbon dioxide to carbon in coal is 3:1, the PH value of the mixture is 7.0 afte...
PUM
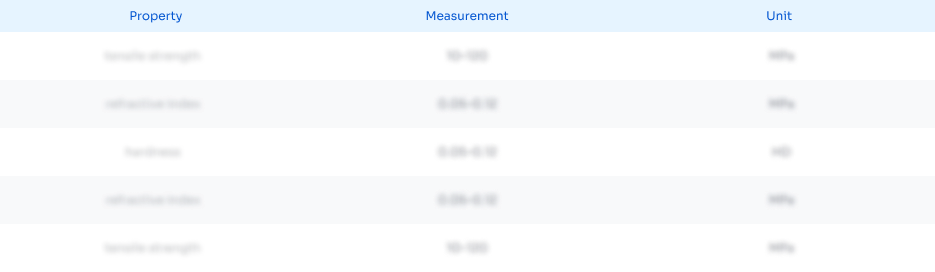
Abstract
Description
Claims
Application Information

- R&D
- Intellectual Property
- Life Sciences
- Materials
- Tech Scout
- Unparalleled Data Quality
- Higher Quality Content
- 60% Fewer Hallucinations
Browse by: Latest US Patents, China's latest patents, Technical Efficacy Thesaurus, Application Domain, Technology Topic, Popular Technical Reports.
© 2025 PatSnap. All rights reserved.Legal|Privacy policy|Modern Slavery Act Transparency Statement|Sitemap|About US| Contact US: help@patsnap.com