A Method for Extracting Feature Information of Fault Signals of Aeroengine Rotor System
A technology for aero-engine and system failures, applied in the direction of engine testing, machine/structural component testing, instruments, etc. Single and other issues
- Summary
- Abstract
- Description
- Claims
- Application Information
AI Technical Summary
Problems solved by technology
Method used
Image
Examples
Embodiment example
[0072] An implementation case of the method for extracting characteristic information of the fault signal of the aeroengine rotor system, including the following process:
[0073] The first step is to collect the rubbing vibration signal of the aero-engine rotor; through the eddy current displacement sensor, select 1000 sets of rubbing vibration signal data samples of the aero-engine rotor at a speed of 2000r / min, and set the sampling frequency of the signal to 1000Hz;
[0074] by formula Construct FM and AM timing simulation signal x 1 (t), simulated signal x 1 (t) contains a non-linear frequency modulation signal x 11 (t) and a frequency-modulated amplitude-modulated signal x with a certain period 12 (t), the sampling frequency of the set signal is 1000Hz;
[0075] signal x 1 The time-domain waveform of (t) is as follows figure 1 shown. Among them, the signal x 1 The waveform diagram of (t) presents complex waveform pulse characteristics without significant periodic...
PUM
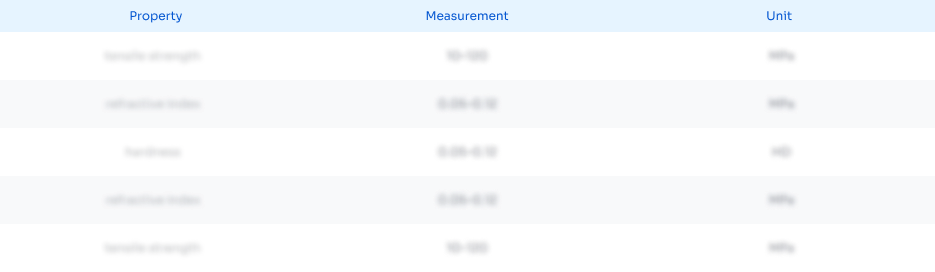
Abstract
Description
Claims
Application Information

- R&D
- Intellectual Property
- Life Sciences
- Materials
- Tech Scout
- Unparalleled Data Quality
- Higher Quality Content
- 60% Fewer Hallucinations
Browse by: Latest US Patents, China's latest patents, Technical Efficacy Thesaurus, Application Domain, Technology Topic, Popular Technical Reports.
© 2025 PatSnap. All rights reserved.Legal|Privacy policy|Modern Slavery Act Transparency Statement|Sitemap|About US| Contact US: help@patsnap.com