A kind of preparation method of epoxy curing agent
A technology of epoxy curing agent and catalyst, which is applied in the direction of epoxy resin coatings and coatings, and can solve the problems of short service life, poor performance, and low gloss of the coating film
- Summary
- Abstract
- Description
- Claims
- Application Information
AI Technical Summary
Problems solved by technology
Method used
Image
Examples
preparation example Construction
[0017] The invention provides a preparation method of an epoxy curing agent. The method comprises the following steps: (1) Weighing an appropriate amount of epoxy resin, organic phenol and catalyst into a reaction vessel, heating to 75-250 DEG C for 0.5-7 hours After that, the temperature is lowered to 30-120° C. and part of the solvent is added to obtain the adduct of epoxy resin and organic phenol and then discharged. Preferably, the heating temperature is 90-200°C, the holding time is 1-5 hours, and the cooling temperature is 40-100°C. By introducing organic phenols, it is beneficial to improve the flexibility and water resistance of the curing agent.
[0018] (2) in above-mentioned reaction vessel, add amine material and partial solvent and be warmed up to 40-125 ℃, slowly drip the adduct of epoxy resin and organic phenol obtained in step (1) under stirring state, at 70-125 ℃ Incubate at 135°C for 0.4-6 hours. Preferably, the heating temperature is 50-120° C., the heat p...
Embodiment 1
[0030] (1) Add 35 grams of E51 epoxy resin, 22 grams of cardanol, and 0.1 grams of N,N dimethylbenzylamine to the there-necked flask, heat up to 100°C for 2h, cool to 80°C and add 10 grams of glycidyl tertiary carbonate ether, and discharging after obtaining the adduct of epoxy resin and cardanol;
[0031] (2) 20 grams of diethylenetriamine were added to the there-necked flask, and 5 grams of ethylene glycol monobutyl ether were heated to 70° C., then the product synthesized in the step (1) was added dropwise, and the dripping was completed at 80° C. for 2h;
[0032] (3) Slowly add 8 grams of water and stir for 30 minutes to obtain epoxy curing agent.
Embodiment 2
[0034] (1) Add 20 grams of bisphenol F-type epoxy resin (NPEF170), 37 grams of petroleum phenol, 0.05 grams of N,N dimethylbenzylamine to the there-necked bottle, heat up to 90°C for 1 hour, cool to 40°C and add 15 g ethylene glycol monobutyl ether, and discharging after obtaining the adduct of epoxy resin and petroleum phenol;
[0035] (2) 20 grams of tetraethylene pentamine was added to the there-necked flask, and 60 grams of ethylene glycol monobutyl ether was heated to 50° C., and then the product synthesized in the step (1) was added dropwise, and the dripping was completed at 100° C. for 1 h;
[0036] (3) Slowly add 40 grams of glacial acetic acid and stir for 30 minutes to obtain epoxy curing agent.
PUM
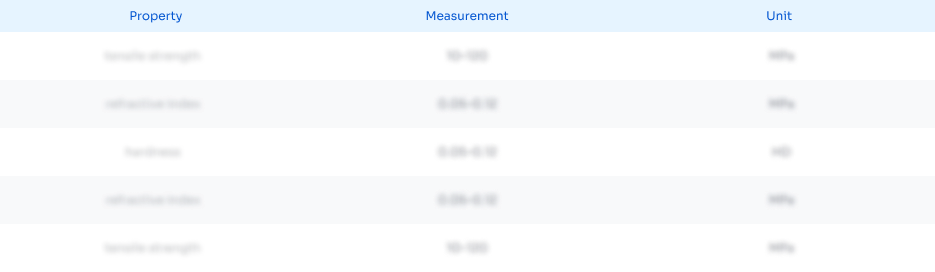
Abstract
Description
Claims
Application Information

- R&D Engineer
- R&D Manager
- IP Professional
- Industry Leading Data Capabilities
- Powerful AI technology
- Patent DNA Extraction
Browse by: Latest US Patents, China's latest patents, Technical Efficacy Thesaurus, Application Domain, Technology Topic, Popular Technical Reports.
© 2024 PatSnap. All rights reserved.Legal|Privacy policy|Modern Slavery Act Transparency Statement|Sitemap|About US| Contact US: help@patsnap.com