Dry method production process for ancient building encaustic tile
A production process and technology of glazed tiles, which are applied in the production, application, and household appliances of ceramic materials, etc., can solve problems such as long dehydration time, easy deformation of products, and large amount of dehydration of tile billets, so as to improve processing efficiency and shorten processing time.
- Summary
- Abstract
- Description
- Claims
- Application Information
AI Technical Summary
Problems solved by technology
Method used
Image
Examples
Embodiment 1
[0062] The invention discloses a dry production process for ancient building glazed tiles, which specifically includes the following steps:
[0063] S1: Prepare materials: Prepare body raw materials, glaze raw materials and accelerators.
[0064] Wherein, green body raw material comprises following weight parts raw material:
[0065]
[0066] Its mixing method is:
[0067] A1: each raw material is ground to 40-60 mesh fine particles and then sieved, and the sieve residue of each raw material is 0.1wt%;
[0068] A2: add the blender after the sieved fly ash and building fine sand are measured, and make it mix evenly;
[0069]A3: Add the sieved loess and red mud to the blender after measuring, and mix evenly again.
[0070] The glaze material comprises the following raw materials in parts by weight:
[0071] Zircon-based pigment 38 parts
[0072] Tantalumite 6 parts
[0073] Loess 8 parts
[0074] Wherein, the zircon-based pigment can be one of vanadium blue, praseodymi...
Embodiment 2
[0094] The invention discloses a dry production process for ancient building glazed tiles, which specifically includes the following steps:
[0095] S1: Prepare materials: Prepare body raw materials, glaze raw materials and accelerators.
[0096] Wherein, green body raw material comprises following weight parts raw material:
[0097]
[0098] Its mixing method is:
[0099] A1: each raw material is ground to 40-60 mesh fine particles and then sieved, and the sieve residue of each raw material is 0.3wt%;
[0100] A2: add the blender after the sieved fly ash and building fine sand are measured, and make it mix evenly;
[0101] A3: Add the sieved loess and red mud to the blender after measuring, and mix evenly again.
[0102] The glaze material comprises the following raw materials in parts by weight:
[0103] Zircon-based pigment 42 parts
[0104] Tantalumite 7 parts
[0105] Loess 9 parts
[0106] Wherein, the zircon-based pigment can be one of vanadium blue, praseodym...
Embodiment 3
[0126] The invention discloses a dry production process for ancient building glazed tiles, which specifically includes the following steps:
[0127] S1: Prepare materials: Prepare body raw materials, glaze raw materials and accelerators.
[0128] Wherein, green body raw material comprises following weight parts raw material:
[0129]
[0130] Its mixing method is:
[0131] A1: each raw material is ground to 40-60 mesh fine particles and then sieved, and the sieve residue of each raw material is 0.5wt%;
[0132] A2: add the blender after the sieved fly ash and building fine sand are measured, and make it mix evenly;
[0133] A3: Add the sieved loess and red mud to the blender after measuring, and mix evenly again.
[0134] The glaze material comprises the following raw materials in parts by weight:
[0135] Zircon-based pigment 45 parts
[0136] Tantalumite 8 parts
[0137] Loess 10 parts
[0138] Wherein, the zircon-based pigment can be one of vanadium blue, praseody...
PUM
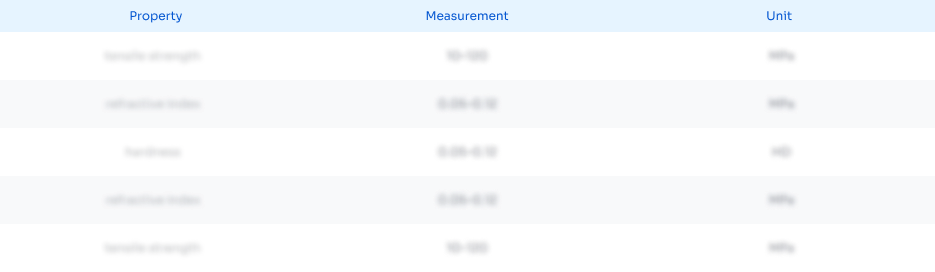
Abstract
Description
Claims
Application Information

- R&D Engineer
- R&D Manager
- IP Professional
- Industry Leading Data Capabilities
- Powerful AI technology
- Patent DNA Extraction
Browse by: Latest US Patents, China's latest patents, Technical Efficacy Thesaurus, Application Domain, Technology Topic, Popular Technical Reports.
© 2024 PatSnap. All rights reserved.Legal|Privacy policy|Modern Slavery Act Transparency Statement|Sitemap|About US| Contact US: help@patsnap.com