Magnetite high-pressure roller mill-wet type preconcentration-stage grinding-tower mill magnetic separation technology
A high-pressure roller grinding and stage grinding technology, applied in the field of magnetite high-pressure rollers, can solve the problems of unstable process, many crushing stages, and high beneficiation cost, and achieves improved grinding fineness, simplified technological process, and significant economic benefits. Effect
- Summary
- Abstract
- Description
- Claims
- Application Information
AI Technical Summary
Problems solved by technology
Method used
Image
Examples
Embodiment 1
[0037] like figure 2 Shown: magnetite high pressure roller mill of the present invention-wet type pre-selection-stage grinding-tower mill magnetic separation process,
[0038] Including coarse crushing operation and intermediate crushing operation, it is characterized in that it also includes the following steps:
[0039] 1) Feed the secondary crushing product with a grade of 31.5% and a particle size of 25mm to 0 mm into a closed-circuit high-pressure roller mill-screening operation consisting of a high-pressure roller mill and a screening device. The high-pressure roller mill is GLGY -06025H type roller mill to obtain high-pressure roller mill-screened products with a particle size of -3mm;
[0040] 2) Feed the high-pressure roller mill-screened product into the wet pre-separation magnetic separator to obtain the wet pre-separation magnetic separator concentrate with a grade of 36.5% and the wet pre-separator magnetic separator tailings with a grade of 7.95% and a yield of...
PUM
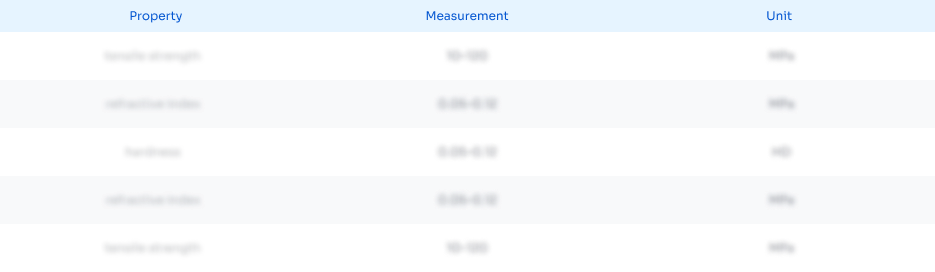
Abstract
Description
Claims
Application Information

- Generate Ideas
- Intellectual Property
- Life Sciences
- Materials
- Tech Scout
- Unparalleled Data Quality
- Higher Quality Content
- 60% Fewer Hallucinations
Browse by: Latest US Patents, China's latest patents, Technical Efficacy Thesaurus, Application Domain, Technology Topic, Popular Technical Reports.
© 2025 PatSnap. All rights reserved.Legal|Privacy policy|Modern Slavery Act Transparency Statement|Sitemap|About US| Contact US: help@patsnap.com