Five-axis numerical control machine tool space error distinguishing method
A space error, CNC machine tool technology, applied to metal processing machinery parts, measuring/indicating equipment, metal processing equipment, etc., can solve problems such as interference errors, unfavorable macro programming, unfavorable automatic compensation, etc.
- Summary
- Abstract
- Description
- Claims
- Application Information
AI Technical Summary
Problems solved by technology
Method used
Image
Examples
Embodiment Construction
[0038] Below in conjunction with specific embodiment, the technical scheme of this patent is described in further detail;
[0039] A method for identifying spatial errors of a five-axis numerically controlled machine tool, comprising the following steps:
[0040] Step 1. Build a ballbar error measurement device with one end fixed on the spindle of the five-axis CNC machine tool and the other end fixed on the center of the rotary table; the ballbar center ball 2 is connected to the spindle through the tool cup 1, and the ballbar sensor ball 5 The sensor ball 5 can measure the real-time length of the ballbar in real time by connecting the center cup 6 with the center seat 7 at the center of the turntable.
[0041] Step 2. Establish a spatial error measurement model according to the ballbar measuring device;
[0042] Step 3. Establish a model experiment, read the theoretical rod length of the ballbar of the CNC lathe and the actual rod length displayed by the ballbar through the...
PUM
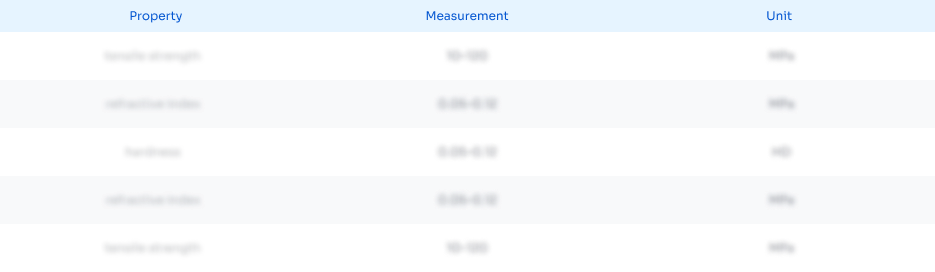
Abstract
Description
Claims
Application Information

- Generate Ideas
- Intellectual Property
- Life Sciences
- Materials
- Tech Scout
- Unparalleled Data Quality
- Higher Quality Content
- 60% Fewer Hallucinations
Browse by: Latest US Patents, China's latest patents, Technical Efficacy Thesaurus, Application Domain, Technology Topic, Popular Technical Reports.
© 2025 PatSnap. All rights reserved.Legal|Privacy policy|Modern Slavery Act Transparency Statement|Sitemap|About US| Contact US: help@patsnap.com