Triaxial Hopkinson rod synchronous dynamic calibrating apparatus and method of three-dimensional impact force sensor
An impact force sensor, synchronous dynamic technology, applied in the direction of measuring devices, instruments, force/torque/work measuring instrument calibration/testing, etc. 3D synchronization calibration and other issues
- Summary
- Abstract
- Description
- Claims
- Application Information
AI Technical Summary
Problems solved by technology
Method used
Image
Examples
Embodiment Construction
[0027] Now in conjunction with embodiment, accompanying drawing, the present invention will be further described:
[0028] The three-axis Hopkinson rod synchronous dynamic calibration device proposed by the present invention includes a launch chamber 1, a launch valve 2, a launch barrel 3, a percussion rod 4, a polytetrafluoroethylene support 5, a pulse shaper 6, and an X-axis incident elastic rod 7. X-axis transmission elastic rod 8, Y-axis transmission elastic rod 9, Z-axis transmission elastic rod 10, strain gauge 11, incident elastic rod electro-hydraulic servo control system 12, transmission elastic rod electro-hydraulic servo control system 13, three-dimensional to be measured Impact sensor 14. The device is a traditional Hopkinson compression rod along the X-axis direction, using a titanium alloy square rod with a cross-section of 20mm*20mm and a length of 2000mm (according to the sensor structure and calibration requirements, hollow square rods or circular cross-sectio...
PUM
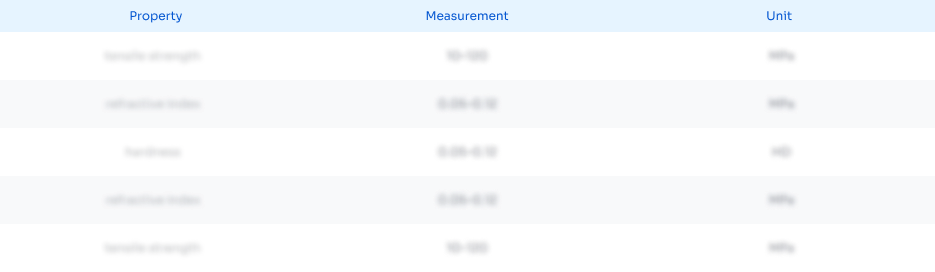
Abstract
Description
Claims
Application Information

- Generate Ideas
- Intellectual Property
- Life Sciences
- Materials
- Tech Scout
- Unparalleled Data Quality
- Higher Quality Content
- 60% Fewer Hallucinations
Browse by: Latest US Patents, China's latest patents, Technical Efficacy Thesaurus, Application Domain, Technology Topic, Popular Technical Reports.
© 2025 PatSnap. All rights reserved.Legal|Privacy policy|Modern Slavery Act Transparency Statement|Sitemap|About US| Contact US: help@patsnap.com