Clamping mechanism for circular electroplating part
A technology of clamping mechanism and electroplating parts, applied in the direction of electrolysis components, electrolysis process, etc., can solve the problems of time-consuming, laborious, troublesome operation, etc., and achieve the effects of easy installation and fixation, convenient electroplating, and simple operation.
- Summary
- Abstract
- Description
- Claims
- Application Information
AI Technical Summary
Problems solved by technology
Method used
Image
Examples
Embodiment Construction
[0020] like figure 1 , figure 2 , image 3 Shown, a kind of clamping mechanism that is used for circular plating piece of the present invention comprises:
[0021] A horizontal support plate 1, the middle part of the upper surface of the support plate 1 is formed with a fixed block 2, the fixed block 2 is screwed on the first lead screw 3, and the lower end of the first lead screw 3 passes through the support Plate 1, the upper end of the first lead screw 3 is connected to the first end of the first coupling 4, the second end of the first coupling 4 is connected to the output shaft of the first stepper motor 5, the The first stepping motor 5 is arranged on the upper surface of the mounting plate 6 . Both ends of the upper surface of the support plate 1 are respectively formed with bearing seats 7, and the two sides of the upper end of the support plate 1 are respectively provided with second screw screws 8, and the first ends of the second screw screws 8 are hinged on the ...
PUM
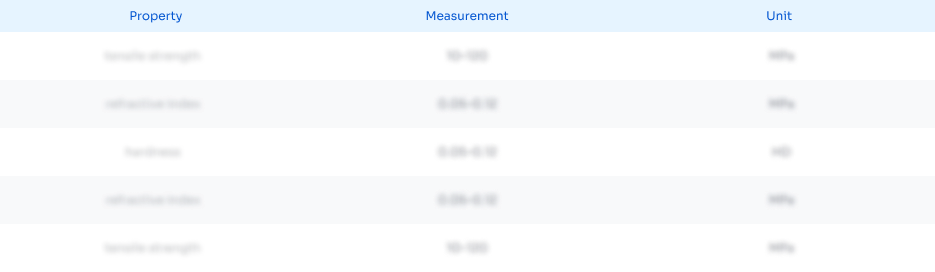
Abstract
Description
Claims
Application Information

- Generate Ideas
- Intellectual Property
- Life Sciences
- Materials
- Tech Scout
- Unparalleled Data Quality
- Higher Quality Content
- 60% Fewer Hallucinations
Browse by: Latest US Patents, China's latest patents, Technical Efficacy Thesaurus, Application Domain, Technology Topic, Popular Technical Reports.
© 2025 PatSnap. All rights reserved.Legal|Privacy policy|Modern Slavery Act Transparency Statement|Sitemap|About US| Contact US: help@patsnap.com