End supporting joint structure for steel bar truss plates crossing frame structure
A steel truss and frame structure technology, which is applied to floors, building components, building structures, etc., can solve the problems of complex installation nodes, low connection strength, low construction efficiency, etc. Simple, smooth node parts
- Summary
- Abstract
- Description
- Claims
- Application Information
AI Technical Summary
Problems solved by technology
Method used
Image
Examples
Embodiment 1
[0034] Such as figure 1 A detachable steel truss panel is shown, which includes a steel truss 1 , a connector 4 , a floor deck 2 and a support 3 . The steel bar truss 1 includes an upper chord steel bar 11 and two lower chord steel bars 12 , and the two lower chord steel bars 12 are respectively welded and connected to the upper chord steel bars 11 through web steel bars 13 . The two lower chord steel bars 12 are connected with the connecting piece 4 relative to each other. The connecting piece 4 includes a slot 41 through the connecting piece 4 with a side opening, and a threaded hole is provided at the lower end of the connecting piece 4 . The connectors 4 are clamped on the two lower chord steel bars 12 in pairs, and each pair of connectors 4 is arranged longitudinally on the steel bar truss 1 . figure 1 The length of the detachable steel truss plate 20 can be designed according to requirements, generally 1-3m, and its width is two steel trusses 2, and in some embodiments...
Embodiment 2
[0050] Such as Figure 7 As shown, the difference between this embodiment and Embodiment 1 is that the frame structure 5 is a frame wall, and formwork 7 is arranged on both sides of the frame wall, and the formwork 7 includes a side formwork 72 on the left side and a side formwork 72 on the right side, The outer side of the formwork is provided with a first support part, and the first support part 81 supports the steel bar truss plate 20 . Since the shear wall does not require the lower formwork, there is no need to erect a support frame.
Embodiment 3
[0052] Such as Figure 8-11 As mentioned above, the difference between this embodiment and Embodiment 1 is that the steel truss panels 20 on both sides of the frame structure 5 have a height difference, so that the forming surface of the upper part of the frame structure 5 and the sides of the frame structure 5 after pouring concrete Floor slabs have different elevations. The upper connecting rib 21 and the lower connecting rib 22 are provided with a first inclined portion 23 and a second inclined portion 24 respectively, and the first inclined portion 23 and the second inclined portion 24 can be located on the same side of the frame structure 5, It can also be the two sides of the frame structure 5 respectively. The first inclined portion 23 and the second inclined portion 24 enable the reinforced truss slabs 20 of different elevations to be well connected to the frame structure 5 , thereby making the poured concrete floor slabs firmly connected to the frame structure.
[0...
PUM
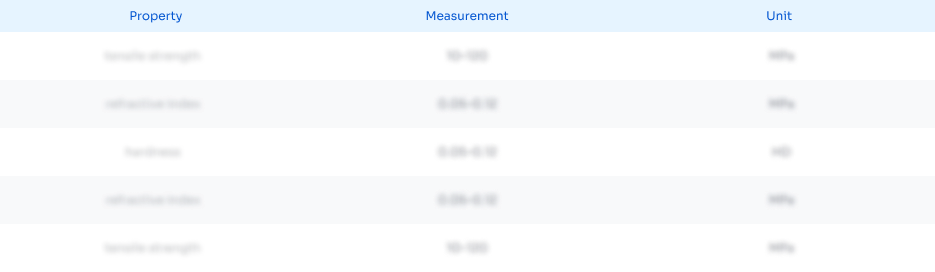
Abstract
Description
Claims
Application Information

- R&D
- Intellectual Property
- Life Sciences
- Materials
- Tech Scout
- Unparalleled Data Quality
- Higher Quality Content
- 60% Fewer Hallucinations
Browse by: Latest US Patents, China's latest patents, Technical Efficacy Thesaurus, Application Domain, Technology Topic, Popular Technical Reports.
© 2025 PatSnap. All rights reserved.Legal|Privacy policy|Modern Slavery Act Transparency Statement|Sitemap|About US| Contact US: help@patsnap.com