Preparation method of organic-inorganic composite concrete retarder
An inorganic composite and retarder technology, applied in the field of retarders, can solve the problems of poor retarding effect and restraining the application range of concrete retarders, etc.
- Summary
- Abstract
- Description
- Claims
- Application Information
AI Technical Summary
Problems solved by technology
Method used
Image
Examples
preparation example Construction
[0022] The present invention also provides a kind of preparation method of organic-inorganic composite concrete retarder, comprises the following steps:
[0023] (1) Calcining bentonite at 300-450°C for 2-4 hours, then milling the calcined bentonite and hydroxyethylidene diphosphonic acid in a ball mill, then adding water and maleic anhydride, and then heating at 80-95°C Ultrasonic reaction for 5-10 hours to obtain modified bentonite;
[0024] (2) After mixing polyether polyol, acid anhydride with 4-8 carbon atoms and organic amine in water, react at 80-120°C for 2-4 hours to obtain polymer emulsion A, and add phosphoric acid to polymer emulsion A Salt retarder, catalyst and formaldehyde are reacted at 80-120°C for 1-4 hours to obtain a retarder intermediate;
[0025] (3) After adding unsaturated glyceride, sodium borate, calcium sulfate, dispersant, surfactant, and modified bentonite to the retarder intermediate and mixing evenly, adjust the concentration of the product obta...
Embodiment 1
[0030] An organic-inorganic composite concrete retarder, made of the following raw materials in parts by weight: 30kg glycidyl methacrylate, 10kg sodium dipolyphosphate, 2kg hydroxyethylidene diphosphonic acid, 5kg bentonite, ethylenediaminetetra Disodium acetate 4kg, polyether 30503kg, 6kg maleic anhydride, 3kg ethylenediamine, 3kg hydrochloric acid (32wt%), 1kg formaldehyde, 3kg sodium borate, 6kg calcium sulfate, 2kg lignosulfonate sodium, 0.8kg organosilicon surface active Agent (purchased from Hangzhou Pinying New Material Co., Ltd., PY402).
[0031] The preparation steps of described organic-inorganic composite concrete retarder are as follows:
[0032] (1) Calcining bentonite at 350°C for 2h, then milling the calcined bentonite and hydroxyethylidene diphosphonic acid in a ball mill, then adding water and maleic anhydride, and then ultrasonically reacting at 90°C for 6h to obtain Modified bentonite;
[0033] (2) After mixing polyether 3050, maleic anhydride and ethylen...
Embodiment 2
[0036]An organic-inorganic composite concrete retarder, made of the following raw materials in parts by weight: 35kg glycidyl methacrylate, 8kg dibutyl phosphate, 4kg hydroxyethylidene diphosphonic acid, 10kg bentonite, 5kg ethylenediamine Disodium tetraacetate, 5kg polyether 3050, 8kg maleic anhydride, 6kg pentaethylene hexamine, 3kg hydrochloric acid (32wt%), 2kg formaldehyde, 4kg sodium borate, 8kg calcium sulfate, 3kg sodium lignosulfonate, 0.5kg organic silicon Surfactant (purchased from Hangzhou Pinying New Material Co., Ltd., PY402).
[0037] The preparation steps of described organic-inorganic composite concrete retarder are as follows:
[0038] (1) Calcining bentonite at 350°C for 3 hours, then milling the calcined bentonite and hydroxyethylidene diphosphonic acid in a ball mill, then adding water and maleic anhydride, and then ultrasonically reacting at 90°C for 8 hours to obtain Modified bentonite;
[0039] (2) After mixing polyether 3050, maleic anhydride and pen...
PUM
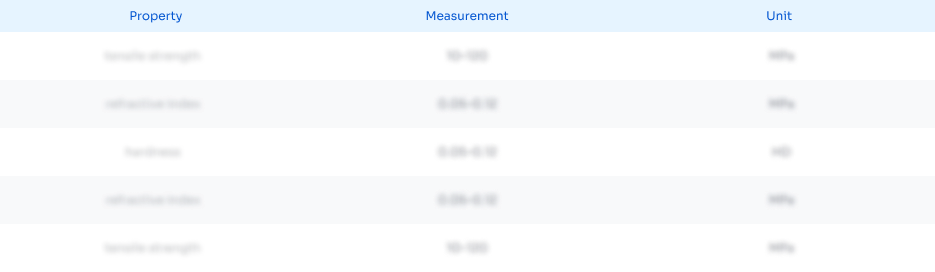
Abstract
Description
Claims
Application Information

- Generate Ideas
- Intellectual Property
- Life Sciences
- Materials
- Tech Scout
- Unparalleled Data Quality
- Higher Quality Content
- 60% Fewer Hallucinations
Browse by: Latest US Patents, China's latest patents, Technical Efficacy Thesaurus, Application Domain, Technology Topic, Popular Technical Reports.
© 2025 PatSnap. All rights reserved.Legal|Privacy policy|Modern Slavery Act Transparency Statement|Sitemap|About US| Contact US: help@patsnap.com