Self-balanced transport vehicle
A transport vehicle and self-balancing technology, applied in the field of vehicle engineering, can solve the problems of complex structure, high cost, complex structure of the center of gravity adjustment system, etc., and achieve the effect of overcoming the risk of rollover
- Summary
- Abstract
- Description
- Claims
- Application Information
AI Technical Summary
Problems solved by technology
Method used
Image
Examples
Embodiment 1
[0018] Such as Figure 1-3 As shown, a self-balancing transport vehicle includes a compartment 1, an underframe 2, a first hydraulic cylinder 3, a second hydraulic cylinder 4, a hydraulic pump 10, a three-way solenoid valve 11, a first solenoid valve 12, and a second solenoid valve 13, oil storage tank 14, pressure sensor 9 and controller. The middle part of compartment 1 is welded by channel steel along the traveling direction of the transport vehicle to form a cuboid bump 5, the two ends of the bottom of compartment 1 perpendicular to the traveling direction of the transport vehicle protrude downwards to form sliders (8, 8'), and the two ends of the chassis 2 The upper part corresponding to the slide block (8, 8') has two guide rails 7 ( figure 2 Only one of the ends is shown in ), the slider extends into (8, 8') guide rail 7 and slides a certain distance in the guide rail 7 with the left and right movement of the compartment, and the slider (8, 8') is far from the inner e...
PUM
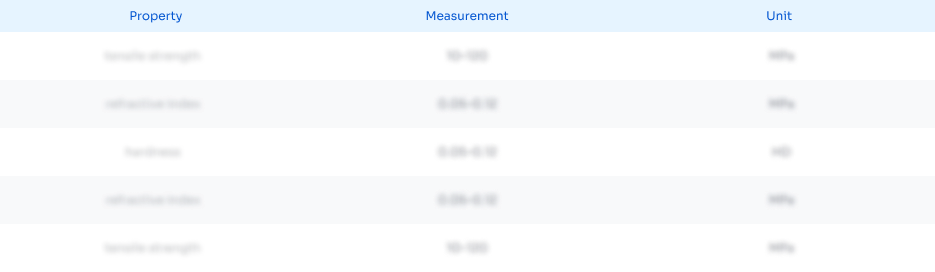
Abstract
Description
Claims
Application Information

- Generate Ideas
- Intellectual Property
- Life Sciences
- Materials
- Tech Scout
- Unparalleled Data Quality
- Higher Quality Content
- 60% Fewer Hallucinations
Browse by: Latest US Patents, China's latest patents, Technical Efficacy Thesaurus, Application Domain, Technology Topic, Popular Technical Reports.
© 2025 PatSnap. All rights reserved.Legal|Privacy policy|Modern Slavery Act Transparency Statement|Sitemap|About US| Contact US: help@patsnap.com