Rotor structural robustness design method for widening built-in permanent magnet synchronous motor speed range
A permanent magnet synchronous motor, rotor structure technology, applied in the magnetic circuit shape/style/structure, magnetic circuit rotating parts, magnetic circuit and other directions, can solve the problem that the permanent magnet magnetic field is difficult to decay, the motor load capacity is weakened, and the motor output is reduced. Small problems such as reducing pulsation and cogging torque, expanding the range of constant power speed regulation, and improving the speed range
- Summary
- Abstract
- Description
- Claims
- Application Information
AI Technical Summary
Problems solved by technology
Method used
Image
Examples
Embodiment Construction
[0022] Firstly, the robust design method of the rotor structure for widening the rotational speed range of the interior permanent magnet synchronous motor of the present invention will be briefly described below. Include the following steps:
[0023] Step 1: Determine the initial rotor structure of the motor. Among them, the permanent magnet adopts a single-layer "V" structure;
[0024] The second step: Determine the Taguchi method as a method for the robust design of the rotor structure to broaden the speed range of the interior permanent magnet synchronous motor;
[0025] Step 3: Improve the rotor structure of the motor. First, under the premise of ensuring that the amount of permanent magnets remains unchanged, segment the "V"-shaped permanent magnets. Each part of the permanent magnets is divided into n segments, and the segmented positions are uneven. The d-axis inductance is effectively increased; at the same time, a protrusion in the direction of the air gap is set on...
PUM
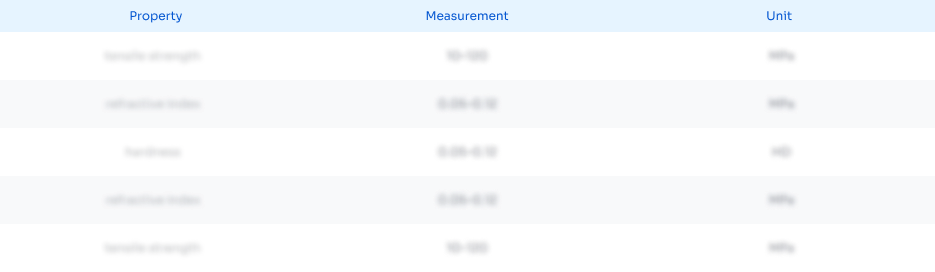
Abstract
Description
Claims
Application Information

- R&D
- Intellectual Property
- Life Sciences
- Materials
- Tech Scout
- Unparalleled Data Quality
- Higher Quality Content
- 60% Fewer Hallucinations
Browse by: Latest US Patents, China's latest patents, Technical Efficacy Thesaurus, Application Domain, Technology Topic, Popular Technical Reports.
© 2025 PatSnap. All rights reserved.Legal|Privacy policy|Modern Slavery Act Transparency Statement|Sitemap|About US| Contact US: help@patsnap.com