Large spur gear online welding repairing process
A welding repair and spur gear technology, applied in welding equipment, manufacturing tools, metal processing equipment, etc., can solve the problems of large vibration and noise, long cycle, rare and other problems of tire rolling mills, reduce downtime losses, reduce maintenance costs, The effect of saving maintenance time
- Summary
- Abstract
- Description
- Claims
- Application Information
AI Technical Summary
Problems solved by technology
Method used
Image
Examples
Embodiment Construction
[0032] The present invention will be further described below in conjunction with specific embodiments.
[0033] refer to figure 1 , figure 2 , image 3 , Figure 4 , Figure 5 As shown, a large-scale spur gear online welding repair process is characterized in that the process is carried out according to the following steps:
[0034] Step 1 Preparation before welding
[0035] 1) On-site construction conditions: Turn off the water supply and power supply system of all tire rolling mills, remove the parts around the large spur gear 1, open the semicircular upper part of the box to expose the large spur gear 1, move the broken teeth to the horizontal position, and clean them with Clean up the surrounding area of the broken teeth and the nearby box with cleaning agent. In addition, there is no draft in the welding place and equipped with lighting facilities and fire extinguishing equipment for night construction;
[0036] 2) Heating device: oxygen acetylene bottle, electri...
PUM
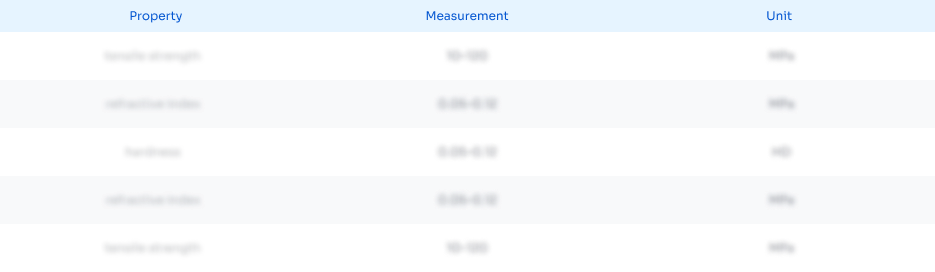
Abstract
Description
Claims
Application Information

- R&D Engineer
- R&D Manager
- IP Professional
- Industry Leading Data Capabilities
- Powerful AI technology
- Patent DNA Extraction
Browse by: Latest US Patents, China's latest patents, Technical Efficacy Thesaurus, Application Domain, Technology Topic, Popular Technical Reports.
© 2024 PatSnap. All rights reserved.Legal|Privacy policy|Modern Slavery Act Transparency Statement|Sitemap|About US| Contact US: help@patsnap.com