Girder type structure crack damage identification method under non-reference data condition
A damage identification, no benchmark technology, applied in character and pattern recognition, computer parts, instruments, etc., can solve problems such as large amount of calculation, high model accuracy requirements, no benchmark data, etc., to achieve the effect of reducing the amount of calculation
- Summary
- Abstract
- Description
- Claims
- Application Information
AI Technical Summary
Problems solved by technology
Method used
Image
Examples
Embodiment 1
[0032] Example 1: In this example, the damage identification experiment is carried out on a reinforced concrete beam with prefabricated crack damage. The crack is located at the mid-span position of the beam, and its depth is 5% of the beam height. In order to obtain the dynamic response signal of the beam, in the experiment The beam is stimulated by hammering. In the experiment, the signal acquisition time is 300 seconds, and the sampling frequency is 2kHz;
[0033] Such as figure 1 As shown, a beam structure crack damage identification method without benchmark data, the specific steps are as follows:
[0034] (1) Evenly arrange 11 measuring points at the bottom of the beam, the measuring sensor is a resistance strain gauge, and the distance between each measuring point is 50cm, as figure 2 Shown; the dynamic response signal Si of the acquisition beam j Such as image 3 As shown; due to the similarity of the waveforms of the time-domain signals of each measuring point and...
Embodiment 2
[0045] Embodiment 2: In this embodiment, the damage identification experiment is carried out on the reinforced concrete beam with prefabricated crack damage. The crack is located at the mid-span position of the beam, and its depth is 10% of the beam height. In order to obtain the dynamic response signal of the beam, in the experiment The beam is stimulated by hammering. In the experiment, the signal acquisition time is 300 seconds, and the sampling frequency is 2kHz;
[0046] A crack damage identification method for beam structures without benchmark data, the specific steps are as follows:
[0047] (1) Evenly arrange 11 measuring points at the bottom of the beam, the measuring sensor is a resistance strain gauge, the distance between each measuring point is 50cm, and the dynamic response signal Si of the beam is collected j ;
[0048] (2) For the dynamic response signal Si obtained in step (1) j Perform Fourier transform to obtain the dynamic response signal spectrum;
[00...
Embodiment 3
[0058] Embodiment 3: In this embodiment, the damage identification experiment is carried out on the reinforced concrete beam with prefabricated crack damage. The crack is located at the mid-span position of the beam, and its depth is 15% of the beam height. In order to obtain the dynamic response signal of the beam, in the experiment The beam is stimulated by hammering. In the experiment, the signal acquisition time is 300 seconds, and the sampling frequency is 2kHz;
[0059] A crack damage identification method for beam structures without benchmark data, the specific steps are as follows:
[0060] (1) Evenly arrange 11 measuring points at the bottom of the beam, the measuring sensor is a resistance strain gauge, the distance between each measuring point is 50cm, and the dynamic response signal Si of the beam is collected j ;
[0061] (2) For the dynamic response signal Si obtained in step (1) j Perform Fourier transform to obtain the dynamic response signal spectrum;
[00...
PUM
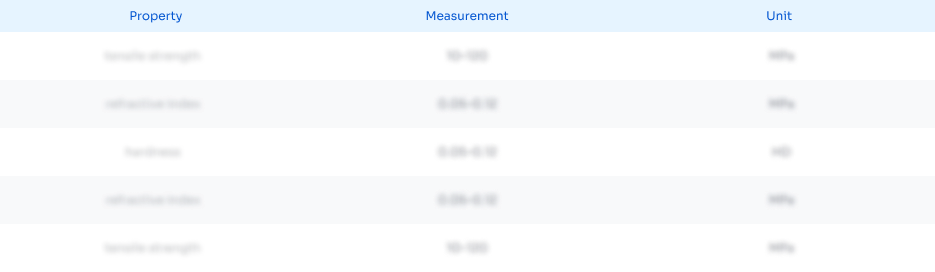
Abstract
Description
Claims
Application Information

- R&D
- Intellectual Property
- Life Sciences
- Materials
- Tech Scout
- Unparalleled Data Quality
- Higher Quality Content
- 60% Fewer Hallucinations
Browse by: Latest US Patents, China's latest patents, Technical Efficacy Thesaurus, Application Domain, Technology Topic, Popular Technical Reports.
© 2025 PatSnap. All rights reserved.Legal|Privacy policy|Modern Slavery Act Transparency Statement|Sitemap|About US| Contact US: help@patsnap.com