Special progressive discharge device for Gleeble-3500 testing machine
A technology of unloading device and testing machine, which is applied in the direction of metal extrusion dies, etc., can solve problems such as difficult unloading procedures, and achieve the effects of simple structure, improved unloading efficiency, and easy operation
- Summary
- Abstract
- Description
- Claims
- Application Information
AI Technical Summary
Problems solved by technology
Method used
Image
Examples
Embodiment 1
[0025] The above-mentioned unloading device and method are used to unload the cup-shaped parts with a diameter of 23 mm after reverse extrusion. The process cycle is 6 minutes per piece, and all the deformed parts are qualified. Compared with the original process, the time is saved by more than 6 times.
[0026] The original process is: take out the entire back-extrusion device after forming, first install the punch with the workpiece on the vise, then take a thin rod to gradually separate the die from the workpiece along the circumference of the die; then clamp Punch, knock the workpiece along the periphery of the cup-shaped part, and take out the workpiece. Basically, after knocking out, the workpiece deforms very seriously along the periphery of the mouth, which seriously affects the analysis of subsequent experimental data; and the unloading process takes more than 40 minutes each .
Embodiment 2
[0028] The above-mentioned unloading device and method are used to unload the cup-shaped parts with a diameter of 23mm after rotary extrusion, the process cycle is 3 minutes per piece, and all the deformed parts are qualified. Compared with the original process, the time saving is more than 13 times.
[0029] The original process is: take out the entire back-extrusion device after forming, first install the punch with the workpiece on the vise, then take a thin rod to gradually separate the die from the workpiece along the circumference of the die; then clamp Punch, knock the workpiece along the periphery of the cup-shaped part, and take out the workpiece. Basically, after knocking out, the workpiece deforms very seriously along the periphery of the mouth, which seriously affects the analysis of subsequent experimental data; and the unloading process takes more than 40 minutes each .
[0030] The unloading device of the specific embodiment of the present invention is simple i...
PUM
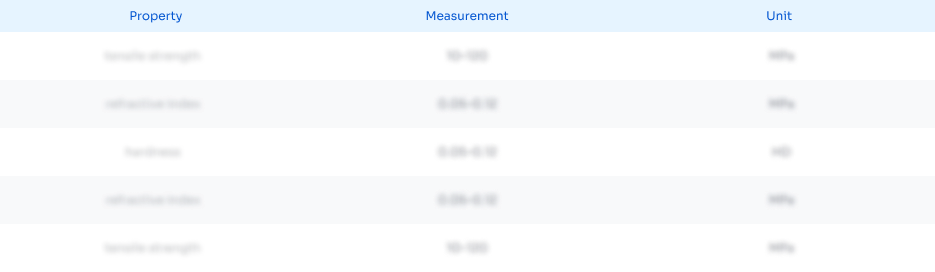
Abstract
Description
Claims
Application Information

- Generate Ideas
- Intellectual Property
- Life Sciences
- Materials
- Tech Scout
- Unparalleled Data Quality
- Higher Quality Content
- 60% Fewer Hallucinations
Browse by: Latest US Patents, China's latest patents, Technical Efficacy Thesaurus, Application Domain, Technology Topic, Popular Technical Reports.
© 2025 PatSnap. All rights reserved.Legal|Privacy policy|Modern Slavery Act Transparency Statement|Sitemap|About US| Contact US: help@patsnap.com