Desizing dyeing and finishing process
A desizing, dyeing and finishing technology, applied in the field of printing and dyeing, can solve the problems of inability to remove impurities in textile materials, increase the difficulty of wastewater treatment, and serious wastewater pollution, so as to improve pollution and damage, reduce the number of refining times, and reduce refining liquid and the effect of energy consumption
- Summary
- Abstract
- Description
- Claims
- Application Information
AI Technical Summary
Problems solved by technology
Method used
Image
Examples
Embodiment 1
[0031] This embodiment relates to the desizing and dyeing process of high density taffeta. The density of the high density taffeta used is 250T, including desizing treatment, dyeing treatment, cleaning, dehydration and shaping steps. The specific process is as follows:
[0032] 1. Desizing treatment:
[0033] Refining: put the high-density taffeta white fabric in the jigger, and alternately refine it in refining solution A and refining solution B successively for 4 times, that is, the refining process is refining solution A-refining solution B-refining solution A-refining For liquid B, the refining temperature is 102°C, the refining bath ratio is 1:35, and the refining time is 25min / time.
[0034] Among them, refining liquid A is composed of 55 g / L of liquid caustic soda with a mass percentage of 10%, 1.8 g / L of desizing agent, 1 g / L of dispersant, 0.05 g / L of penetrating agent and water. The desizing agent used in this embodiment is commercially available desizing agent HS-123...
Embodiment 2
[0043] The main difference between this example and Example 1 is that the refining solution B in the desizing treatment in step 1 does not contain camellia saponin.
Embodiment 3
[0045] The difference between this embodiment and Embodiment 1 mainly lies in that in the desizing treatment in step 1, the refining solution A is composed of 50 g / L of liquid caustic soda with a mass percentage of 10%, 1.5 g / L of desizing agent, 1.5 g / L of dispersant, and osmotic Agent 0.05g / L and water composition. Refining liquid B includes ricinoleic acid sulfate sodium salt 5g / L, AEO-9 0.6g / L, tetradecyl dimethyl benzyl ammonium chloride 5.6g / L, fatty acid polyoxyethylene ester 1.6g / L and Camellia saponin 0.4g / L, and the rest is water.
PUM
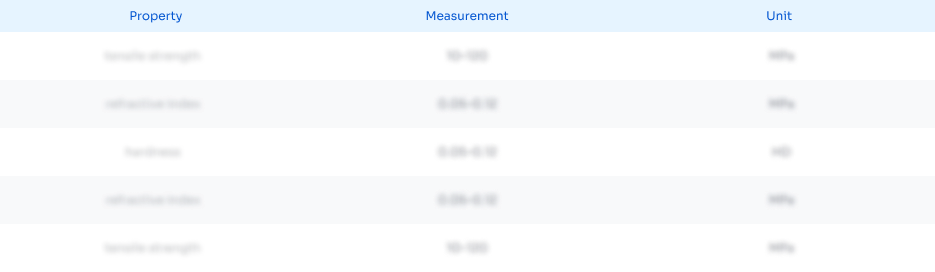
Abstract
Description
Claims
Application Information

- Generate Ideas
- Intellectual Property
- Life Sciences
- Materials
- Tech Scout
- Unparalleled Data Quality
- Higher Quality Content
- 60% Fewer Hallucinations
Browse by: Latest US Patents, China's latest patents, Technical Efficacy Thesaurus, Application Domain, Technology Topic, Popular Technical Reports.
© 2025 PatSnap. All rights reserved.Legal|Privacy policy|Modern Slavery Act Transparency Statement|Sitemap|About US| Contact US: help@patsnap.com