A sintering process homogeneity detection system and method
A sintering process and detection system technology, applied in the sintering field, can solve problems such as sinter quality fluctuations, high ore return volume, instability, etc., to achieve the effect of solving horizontal and vertical unevenness, improving quality and output, and avoiding over-burning
- Summary
- Abstract
- Description
- Claims
- Application Information
AI Technical Summary
Problems solved by technology
Method used
Image
Examples
Embodiment 1
[0034] The protection sleeve 8 has 4 sleeve holes on the side facing the sintered material layer; the front ends of the 4 sampling tubes 9 are penetrated by the opening end of the protection sleeve 8, and respectively pass through the sleeve holes. The area of the upper mouth of the sampling cup is 10mm 2 . The two flue gas sampling devices 4 are respectively installed on the two adjacent bellows 3 just outside the igniter 1 of the machine head, which is called the first sampling group; the two flue gas sampling devices 4 are respectively installed on the penultimate third and On the second bellows 3, it is called the second sampling group. In the first sampling group and the second sampling group, the area at the bottom of the sintering trolley 2 where each sampling tube 9 of the flue gas sampling device 4 is located corresponds to the ignition area of each igniter burner 6 and the control of each cloth auxiliary door 5 respectively. Cutting area.
[0035] The specific...
Embodiment 2
[0047] The protective casing 8 has 6 casing holes; the front ends of the 6 sampling tubes 9 are penetrated through the opening end of the protective casing 8, and then passed through the casing holes respectively. The area of the upper opening of the sampling cup 7 is 3dm2. 3 pieces The flue gas sampling devices 4 are respectively installed on the three adjacent bellows 3 just outside the igniter 1 of the machine head, which is called the first sampling group; the three flue gas sampling devices 4 are respectively installed at the fourth and third from the bottom of the machine tail. and the second bellows 3, called the second sampling group. In the first sampling group and the second sampling group, the area at the bottom of the sintering trolley 2 where each sampling tube 9 of the flue gas sampling device 4 is located corresponds to the ignition area of each igniter burner 6 and the control of each cloth auxiliary door 5 respectively. Cutting area. The flue gas analyzer...
PUM
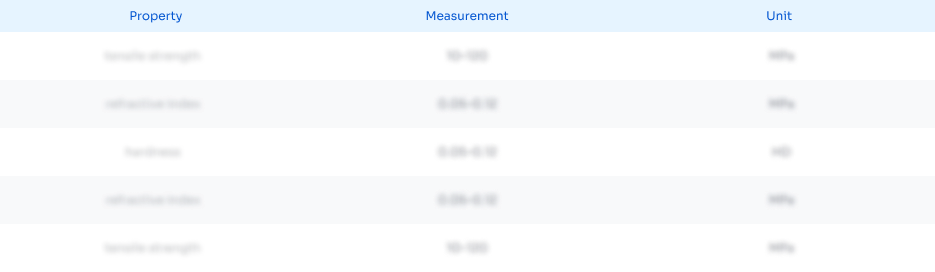
Abstract
Description
Claims
Application Information

- R&D Engineer
- R&D Manager
- IP Professional
- Industry Leading Data Capabilities
- Powerful AI technology
- Patent DNA Extraction
Browse by: Latest US Patents, China's latest patents, Technical Efficacy Thesaurus, Application Domain, Technology Topic, Popular Technical Reports.
© 2024 PatSnap. All rights reserved.Legal|Privacy policy|Modern Slavery Act Transparency Statement|Sitemap|About US| Contact US: help@patsnap.com