A method for testing real-time dynamic stress of disc-type tie-rod combined rotors
A real-time dynamic, test method technology, applied in the direction of measuring force, measuring device, instrument, etc., can solve problems such as not being well solved, and achieve the effect of simple structure, overcoming inaccuracy, and easy installation
- Summary
- Abstract
- Description
- Claims
- Application Information
AI Technical Summary
Problems solved by technology
Method used
Image
Examples
Embodiment Construction
[0024] The present invention is further described below in conjunction with accompanying drawing:
[0025] see figure 1 ,
[0026] A method for testing the real-time dynamic stress of a disc-type tie-rod combined rotor, the disc-type tie-rod combined rotor includes a rotor 2, a tie rod 3, a left disc 41, a middle disc 42, and a right disc 43; the center of one side of the left disc 41 is vertically arranged There is a rotor 2, and the center of one side of the right disc 43 is vertically provided with the rotor 2, the side of the left disc 41 and the right disc 43 without the rotor 2 is arranged oppositely, the middle disc 42 is arranged between the left disc 41 and the right disc 43, and the left disc 41. The middle disk 42 and the right disk 43 are set concentrically; the left disk 41, the middle disk 42 and the right disk 43 are all provided with tie rod holes, and the tie rods 3 pass through the tie rod holes in turn to connect the three disks;
[0027] The method for te...
PUM
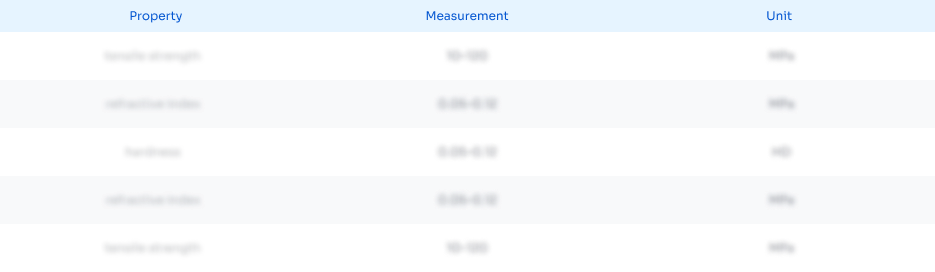
Abstract
Description
Claims
Application Information

- R&D
- Intellectual Property
- Life Sciences
- Materials
- Tech Scout
- Unparalleled Data Quality
- Higher Quality Content
- 60% Fewer Hallucinations
Browse by: Latest US Patents, China's latest patents, Technical Efficacy Thesaurus, Application Domain, Technology Topic, Popular Technical Reports.
© 2025 PatSnap. All rights reserved.Legal|Privacy policy|Modern Slavery Act Transparency Statement|Sitemap|About US| Contact US: help@patsnap.com