Method for preparing high purity molybdenum trioxide by one-step roasting of molybdenite concentrate
A molybdenum trioxide and concentrate technology, applied in the direction of molybdenum oxide/molybdenum hydroxide, etc., can solve the problems of high material requirements, large thermal energy consumption, low molybdenum recovery rate, etc., and achieves good equipment adaptability, convenient waste gas treatment, molybdenum The effect of high recovery rate
- Summary
- Abstract
- Description
- Claims
- Application Information
AI Technical Summary
Benefits of technology
Problems solved by technology
Method used
Image
Examples
Embodiment 1
[0032] Add 10% alumina powder to a high-grade molybdenum fine powder containing Mo 57.36%, Si 0.85%, Ca 0.27%, Fe 0.61%, Al 0.19%, Pb 0.08%, Cu 0.07%, and make The ball obtains a green ball with a diameter of about 8mm and a water content of about 12%, and the cloth is placed on the grate machine with a thickness of about 50mm. First blow in 120°C low-temperature hot air for 10 minutes, and then blow in 950°C high-temperature hot air from bottom to top, and the air volume per square meter is controlled at 300m 3 / h, the mixed steam is pumped into the quench chamber and the solid product is collected through a cloth bag. After 25 minutes, the high-temperature hot air supply was stopped, and the tailings and products were tested, and the product purity was calculated to be higher than 99.9%, and the molybdenum recovery rate was 96.47%.
[0033] If the height of the material layer is increased to 100mm, the air volume per square meter is increased to 350m 3 / h, other conditions...
Embodiment 2
[0035] Add 7% alumina powder to a high-grade molybdenum fine powder containing 55.62% Mo, 1.45% Si, 1.14% Ca, 0.70% Fe, 0.27% Al, 0.10% Pb, and 0.07% Cu. The ball obtains a green ball with a diameter of about 8mm and a water content of about 10%, and the cloth is placed on the grate machine with a thickness of about 50mm. First let in 120°C low-temperature hot air for 10 minutes, and then blow in 1000°C high-temperature hot air from bottom to top, and the air volume per square meter is controlled at 300m 3 / h, the mixed steam is pumped into the quench chamber and the solid product is collected through a cloth bag. After 25 minutes, the high-temperature hot air supply was stopped, and the tailings and products were tested, and the product purity was calculated to be higher than 99.9%, and the molybdenum recovery rate was 91.32%.
Embodiment 3
[0037] Add 5% quartz powder to a medium-grade molybdenum fine powder containing Mo 52.05%, Si 4.85%, REE 1.74%, Ca 1.48%, Fe 0.92%, Pb 0.14%, Cu 0.09%, and make The ball obtains a green ball with a diameter of about 8mm and a water content of about 10%, and the cloth is placed on the grate machine with a thickness of about 50mm. First blow in 120°C low-temperature hot air for 10 minutes, and then blow in 1050°C high-temperature hot air from bottom to top, and the air volume per square meter is controlled at 300m 3 / h, the mixed steam is pumped into the quench chamber and the solid product is collected through a cloth bag. After 30 minutes, the supply of high-temperature hot air was stopped, and the purity of the product was calculated to be higher than 99.8%, and the recovery rate of molybdenum was 85.47%.
[0038] If no plasticizer is added and other process conditions remain unchanged (that is, other condition parameters are consistent with those in Implementation 3), the f...
PUM
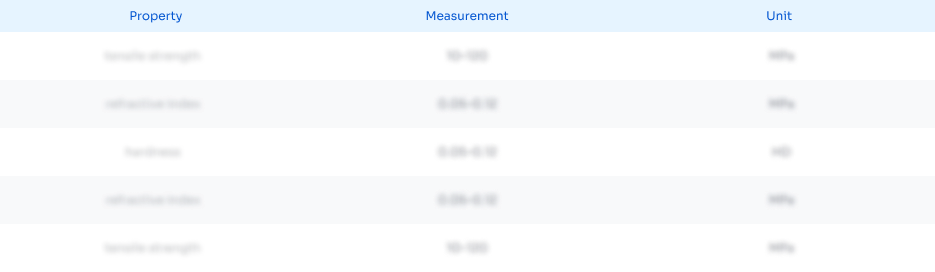
Abstract
Description
Claims
Application Information

- R&D
- Intellectual Property
- Life Sciences
- Materials
- Tech Scout
- Unparalleled Data Quality
- Higher Quality Content
- 60% Fewer Hallucinations
Browse by: Latest US Patents, China's latest patents, Technical Efficacy Thesaurus, Application Domain, Technology Topic, Popular Technical Reports.
© 2025 PatSnap. All rights reserved.Legal|Privacy policy|Modern Slavery Act Transparency Statement|Sitemap|About US| Contact US: help@patsnap.com