Desulphurization and dust removal integral cylinder heating furnace system and desulphurization and dust removal method thereof
A desulfurization and dust removal, heating furnace technology, applied in the direction of chemical instruments and methods, separation methods, gas treatment, etc., can solve the problem that the emission index of sulfur dioxide content cannot meet the requirements of environmental protection regulations, the sulfur content index of flue gas exceeds the limit value of environmental protection regulations, and the flue gas Sulfur content index can not be met and other problems, to achieve the effect of saving process equipment investment, small footprint, convenient operation
- Summary
- Abstract
- Description
- Claims
- Application Information
AI Technical Summary
Problems solved by technology
Method used
Image
Examples
Embodiment Construction
[0022] The specific embodiment of the present invention will be further described below in conjunction with accompanying drawing:
[0023] Such as figure 1 As shown, an integrated cylindrical heating furnace system for desulfurization and dust removal according to the present invention includes a cylindrical heating furnace 1, a combustion chamber is arranged at the bottom of the cylindrical heating furnace 1, and the furnace above the combustion chamber is divided into radiation chambers one by one. Section 11 and convection section 12, the top of cylindrical heating furnace 1 is provided with chimney; The top of described radiant section 11 is provided with dry absorbent injection inlet 111, and dry absorbent injection inlet 111 is connected absorbent injection system by pipeline; The chimney The lower part is the dust removal and desulfurization section 13, and the upper part is the pressurization section 14; the bottom of the dust removal and desulfurization section 13 is ...
PUM
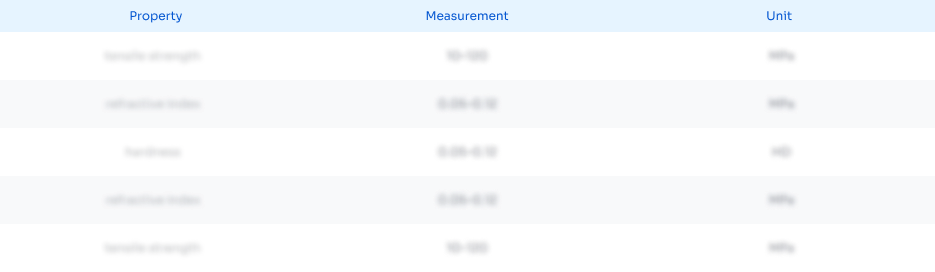
Abstract
Description
Claims
Application Information

- R&D Engineer
- R&D Manager
- IP Professional
- Industry Leading Data Capabilities
- Powerful AI technology
- Patent DNA Extraction
Browse by: Latest US Patents, China's latest patents, Technical Efficacy Thesaurus, Application Domain, Technology Topic, Popular Technical Reports.
© 2024 PatSnap. All rights reserved.Legal|Privacy policy|Modern Slavery Act Transparency Statement|Sitemap|About US| Contact US: help@patsnap.com