A method and device for aluminum-magnesium composite deoxidation alloying
A technology of composite deoxidizing alloy and aluminum-magnesium is applied in the field of iron and steel smelting, which can solve the problems of high price, difficult preparation, poor technical economy and the like, and achieve the effects of convenient operation and simple device structure.
- Summary
- Abstract
- Description
- Claims
- Application Information
AI Technical Summary
Problems solved by technology
Method used
Image
Examples
Embodiment 1
[0057] see figure 1 , The special electrolytic reaction control device of the present invention includes an anode lifting device 1 , an anode 2 , a ladle 5 , a cathode lifting device 6 , a cathode 7 and a DC power supply control device 8 . An anode lifting device 1 is arranged on the upper left side of the ladle 5; the anode lifting device 1 is equipped with high-temperature resistant metal molybdenum ceramic anodes 2, the number is 4, and the anodes 2 are inserted in the slag 3; 2. Adjust the depth of inserting the slag 3 to ensure that the anode 2 is in contact with the slag 3 and not with the molten steel 4; the other side above the ladle 5 is provided with a cathode lifting device 6, and the cathode 7 is installed on the cathode lifting device 6. The cathode 7 is a cylinder with two layers of composite structure inside and outside, the outer layer is wrapped with high temperature resistant cement, and the inside is a graphite rod; the cathode 7 is inserted into the molten ...
Embodiment 2
[0069] The special electrolytic reaction control device of this embodiment is the same as that of Embodiment 1.
[0070] The alumina-rich material used in this example is aluminum ash under the electrolytic aluminum sieve, and its composition is shown in Table 3;
[0071] Table 3 Main chemical composition of aluminum ash under electrolytic aluminum sieve wt%
[0072]
[0073] The magnesium oxide-rich material used in this example is light-burned dolomite, and its composition is shown in Table 4.
[0074] Table 4 The main chemical composition of lightly burned dolomite wt%
[0075]
[0076] Apply this special electrolytic reaction control on 100t ladle for deoxidation alloying operation. The overall control process is: the weight of molten steel in the converter is 103 tons, the C content at the end of smelting is 0.046%, the oxygen content at the end of molten steel is 0.061% (percentage by weight), the temperature of molten steel at the end of smelting is 1707°C; Add...
Embodiment 3
[0079] The special electrolytic reaction control device of this embodiment is the same as that of Embodiment 1.
[0080] The alumina-rich material used in this embodiment is aluminum slag, and its composition is as shown in Table 5;
[0081] Table 5 Main chemical composition of aluminum slag wt%
[0082]
[0083] The magnesium oxide-rich material used in this example is dead-burned magnesium, and its composition is shown in Table 6.
[0084] Table 6 Main chemical composition of dead-burned magnesium wt%
[0085]
[0086] Apply this special electrolytic reaction control on 100t ladle for deoxidation alloying operation. The overall control process is: the weight of molten steel in the converter is 98 tons, the C content at the end of smelting is 0.052%, the oxygen content at the end of molten steel is 0.048% (percentage by weight), the temperature of molten steel at the end of smelting is 1688°C; Add aluminum slag and dead-burned magnesium to molten steel; the amount of...
PUM
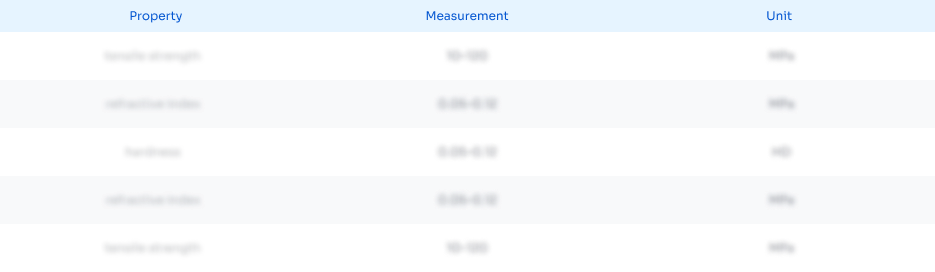
Abstract
Description
Claims
Application Information

- Generate Ideas
- Intellectual Property
- Life Sciences
- Materials
- Tech Scout
- Unparalleled Data Quality
- Higher Quality Content
- 60% Fewer Hallucinations
Browse by: Latest US Patents, China's latest patents, Technical Efficacy Thesaurus, Application Domain, Technology Topic, Popular Technical Reports.
© 2025 PatSnap. All rights reserved.Legal|Privacy policy|Modern Slavery Act Transparency Statement|Sitemap|About US| Contact US: help@patsnap.com