Method and device for jointly calibrating robot and three-dimensional sensing component
A sensor component and joint calibration technology, applied in the field of three-dimensional measurement, can solve the problem of low matching accuracy of calibration results, and achieve the effect of improving matching accuracy
- Summary
- Abstract
- Description
- Claims
- Application Information
AI Technical Summary
Problems solved by technology
Method used
Image
Examples
Embodiment Construction
[0042] In order to make the purpose, technical solution and advantages of the present application clearer, the present application will be further described in detail below in conjunction with the accompanying drawings and embodiments. It should be understood that the specific embodiments described here are only used to explain the present application, and are not intended to limit the present application.
[0043] The joint calibration method of robot and three-dimensional sensing components provided by this application can be applied to such as figure 1 shown in the application environment. Wherein, the terminal 102 communicates with the server 104 through the network. Obtain the target reference point information, the transformation relationship of the first coordinate system, the transformation relationship of the third coordinate system and the transformation relationship of the second coordinate system corresponding to the robot in different postures through the termina...
PUM
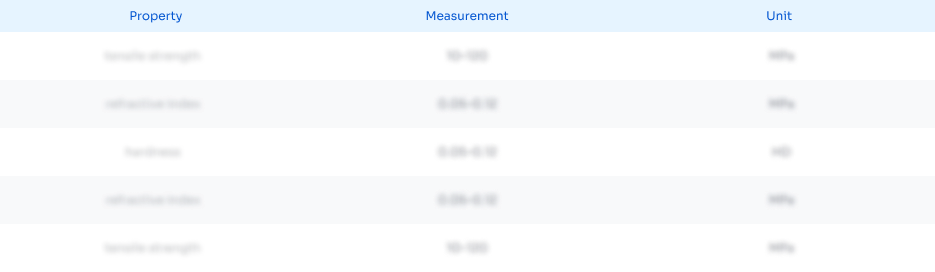
Abstract
Description
Claims
Application Information

- R&D
- Intellectual Property
- Life Sciences
- Materials
- Tech Scout
- Unparalleled Data Quality
- Higher Quality Content
- 60% Fewer Hallucinations
Browse by: Latest US Patents, China's latest patents, Technical Efficacy Thesaurus, Application Domain, Technology Topic, Popular Technical Reports.
© 2025 PatSnap. All rights reserved.Legal|Privacy policy|Modern Slavery Act Transparency Statement|Sitemap|About US| Contact US: help@patsnap.com