A printing path generation method for metal additive manufacturing
A printing path and metal additive technology, applied in the field of 3D printing, can solve problems such as reducing residual stress, achieve the effects of reducing residual stress, reducing shrinkage deformation, and reducing aggregation effect
- Summary
- Abstract
- Description
- Claims
- Application Information
AI Technical Summary
Problems solved by technology
Method used
Image
Examples
Embodiment 1
[0030] figure 1 The flow chart of the printing path generation method of the aperiodic symmetric structure provided by Embodiment 1 of the present invention is mainly used for generating the printing path of the aperiodic symmetric rotating part in the metal additive manufacturing process. The printing path generation method provided by Embodiment 1 of the present invention is based on the idea of random distribution, and uses the randomness of the printing path to make the direction of the internal stress generated during the printing and scanning cooling process divergent, so that the stress values generated at various places on the printed piece It presents a uniform distribution state, reduces the stress accumulation effect of the printed parts, reduces the residual stress, and improves the molding quality of metal manufacturing.
[0031] Specifically, such as figure 1 As shown, for a non-periodic symmetrical structure, the printing path generation method provided by ...
Embodiment 2
[0049] image 3 The flow chart of the method for generating the printing path of the periodic symmetric structure provided by the second embodiment of the present invention is mainly used for generating the printing path of the periodic symmetric structure in the metal additive manufacturing process. Same as the first embodiment, the printing path generation method provided by the second embodiment is also based on the idea of random distribution, and some steps are the same as those in the first embodiment, and the same steps as the first embodiment will not be repeated in the second embodiment.
[0050] In this embodiment, the periodic symmetric structure refers to a structure in which the rotated structure can overlap with the structure before rotation after rotating a preset angle. The smallest substructure of the distribution is called a periodic symmetric unit, that is, after each periodic symmetric unit is rotated by a preset angle, it coincides with the adjacent peri...
PUM
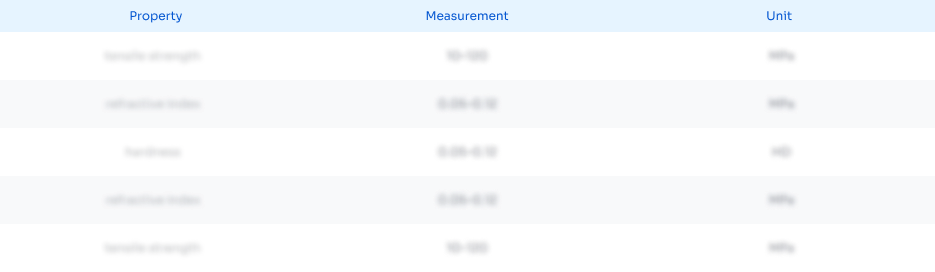
Abstract
Description
Claims
Application Information

- Generate Ideas
- Intellectual Property
- Life Sciences
- Materials
- Tech Scout
- Unparalleled Data Quality
- Higher Quality Content
- 60% Fewer Hallucinations
Browse by: Latest US Patents, China's latest patents, Technical Efficacy Thesaurus, Application Domain, Technology Topic, Popular Technical Reports.
© 2025 PatSnap. All rights reserved.Legal|Privacy policy|Modern Slavery Act Transparency Statement|Sitemap|About US| Contact US: help@patsnap.com